What does AFMEA mean in SOFTWARE
Advanced Failure Modes and Effects Analysis (AFMEA) is a type of quality assurance used to manage risk in the development process. It's an iterative process used to identify potential failure modes and their causes, then determine the corrective action needed for each failure mode. The goal of AFMEA is to reduce the likelihood of system failures by identifying design and manufacturing defects before they become problems. AFMEA is often executed during a system's initial design phase, but it can be applied at any point during product life cycle for greatly improving product reliability.
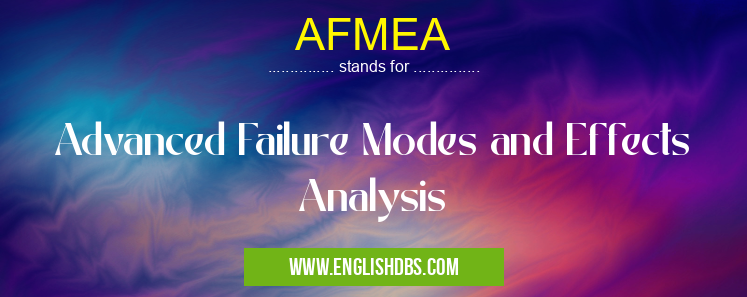
AFMEA meaning in Software in Computing
AFMEA mostly used in an acronym Software in Category Computing that means Advanced Failure Modes and Effects Analysis
Shorthand: AFMEA,
Full Form: Advanced Failure Modes and Effects Analysis
For more information of "Advanced Failure Modes and Effects Analysis", see the section below.
Essential Questions and Answers on Advanced Failure Modes and Effects Analysis in "COMPUTING»SOFTWARE"
What is Advanced Failure Modes and Effects Analysis (AFMEA)?
Advanced Failure Modes and Effects Analysis (AFMEA) is a risk management technique designed to identify the potential causes of failure, analyze their consequences, prioritize actions for avoidance, and develop corrective actions to mitigate the risks. This approach helps teams anticipate what can go wrong, and mitigates the likelihood of failure or its magnitude should it occur.
What are the benefits of using AFMEA?
The primary benefits of employing an Advanced Failure Mode and Effects Analysis process involve predicting potential modes of failure across a system, products or services before they happen. By doing so, companies can proactively implement measures in order to minimize any negative effects on quality control, cost savings, customer satisfaction and overall safety.
What are the steps involved in performing an AFMEA?
Steps involved in performing an AFMEA include selecting a product or process; define team members with expertise about that product/process; identify functional requirements; create a failure mode worksheet; analyze each identified failure mode for severity, occurrence and detection; identify corrective action suggestions; assign responsibility for implementation; monitor results after corrective action implementation; continually track system performance over time.
Who should be included in an AFMEA team?
Depending upon the scope of the project at hand, team members may include representatives from Manufacturing Engineering/Operations personnel who understand product design as well as assembly processes used to produce it. Quality Engineers may provide their expertise into current inspection systems used as part of quality control procedures. Other team members may include Service/Maintenance Technicians who repair failed components along with Research & Development Personnel who have knowledge regarding design details which potentially might lead to mode failures when pushed beyond design capabilities.
How do you decide severity ratings during an AFMEA process?
Severity ratings depend upon various factors such as whether the failure affects safety or product performance. Additionally other important criteria such like customer satisfaction or financial losses must also be taken into account while deciding severity ratings during an AFMEA process. As a general rule when assigning these ratings use subjectivity rather than relying solely on hard metrics such as cost or production duration.
How does Risk Priority Number (RPN) help during an AFMEA study?
Risk Priority Number (RPN) is derived by multiplying three parameters namely Severity (S), Occurrence (O) & Detection (D). RPN values assist in correctly identifying the focus areas for improvement making sure that maximum benefit is realized from any given effort invested towards rectifying identified issues. Thus RPN helps prioritize activities related improvement within designated projects hence streamlining resources more effectively.
Who reviews action plans specified in AFMEAs?
Generally all quality systems require specified authority levels within organizations for approving action plans specified during an AFMEAs process. Typically Department Managers review them before passing them onto higher-ups for final approval. It is necessary to maintain good documentation including workflow diagrams with required signatories affixed at every stage ensuring clear communication channels exist between different stakeholders throughout entire lifecycle for successful completion of project.
How does one document outputs from AFMEAs?
Generally designated Centralized Database Systems which allow smooth data transfer among multiple departments including engineering & quality personnel would be helpful when it comes to documenting outputs from a completed legit AFMEMA study chances are records from similar projects might come handy if ever needed in future references.
How do you verify results after taking corrective actions suggested by completing an FMECA?
When verifying results post taking corrective actions suggested by FMECA one needs to determine whether short-term quick wins have been achieved first followed by medium & long-term features related performance enhancements - possibly even improving existing processes leading unexpected returns such as improved efficiency gained through rational decisions that were made initially considering return-on-investment opportunities under consideration