What does ED mean in HARDWARE
Ed (Electro-deposit) is a metallurgic term for the process of electro-plating or coating an object with a metal layer, usually to reduce corrosion. It has a wide range of applications in many different industries, from automotive parts and home appliances to industrial piping and medical implants. ED is mainly used as a protective layer on metal objects, providing them with increased durability and improved wear resistance. It also helps improve product performance by reducing friction and increasing electrical conductivity. With its many advantages comes more complexity compared to other coating methods. The process of ED requires precise control over the chemical reactions that occur, making it an important part of many businesses.
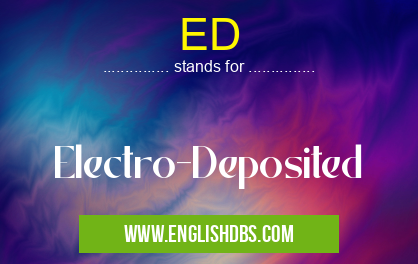
ED meaning in Hardware in Computing
ED mostly used in an acronym Hardware in Category Computing that means Electro-Deposited
Shorthand: ED,
Full Form: Electro-Deposited
For more information of "Electro-Deposited", see the section below.
What Does ED Stand For?
ED stands for Electro-Deposition. This is the process of applying a thin layer of metal onto an object using electricity, resulting in a durable protection from corrosion and other damage caused by everyday use. This gives the object greater overall strength and improved performance in many areas such as friction reduction and electrical conductivity improvement.
How Does ED Work?
ED works by passing an electric current through a liquid electrolyte solution containing positively charged ions (cations) and negatively charged ions (anions). The electric current causes positively charged cations from the solution to be attracted to the negatively charged surface of the object being plated. These cations then form layers on the surface’s surface, thereby resulting in an electroplated coating that is resistant to corrosion and provides increased durability as well as improved performance in some areas such as wear resistance or reduced friction coefficient.
Advantages Of ED
The main advantage of using ED is that it allows for greater precision than other methods such as painting or powder coating because it involves precise control over chemical reactions which can be monitored during the process. This makes it ideal for creating complex patterns or designs on objects requiring intricate detailing or intricate insulation layers that are essential for providing protection against environmental factors such as moisture or chemicals exposure. Additionally, due to its thinness nature when electrodeposited film thicknesses can be extremely small allowing for low energy consumption when applied with thinner coatings also contributing to energy savings since less electricity will be needed for plating thickening films that are thicker than average while still achieving reliable results.
Essential Questions and Answers on Electro-Deposited in "COMPUTING»HARDWARE"
What is Electro-Deposited?
Electro-Depositing (or Electroplating) is a process of coating an electrically conductive surface with a thin layer of metal using electrolysis. It involves passing an electric current through a liquid electrolyte solution, which contains dissolved metal salts, and depositing the metal onto the surface of an electrically conductive component to be plated.
What are the advantages of electro-depositing?
Electo-depositing has numerous advantages including corrosion protection, improved wear resistance, lubricity, electrical insulation, improved aesthetics, reduced friction and increased solderability. Additionally it can be used to coat components for specific applications that require high strength or low electrical resistance properties.
How is electro-deposition performed?
To perform electro-deposition, first correctly prepare the substrate surface by performing chemical or mechanical cleaning processes to remove any impurities before plating begins. Components must then be immersed in the electrolyte solution where a direct current is passed through them resulting in deposition of metal onto the substrate from the solution.
What metals can be electro-deposited?
Many metals such as nickel, zinc and copper can be electro-deposited, however other precious metals such as gold and palladium can also be used in specialized applications. The choice of metal depends on the required application and performance requirements when using these metals for plating purposes.
What are some common applications for electro-Deposition?
Electo-deposition is commonly used in applications in many industries ranging from automotive parts to jewelry making and medical devices. It is primarily used to provide corrosion protection and improve wear resistance or solderability on surfaces such as steel or glass components but can also be applied for more decorative purposes such as jewelry plating or industrial coatings with unique aesthetic characteristics.
What types of tanks are required for electroplating/electro-depositing?
A tank suitable for electo-deposition must contain an electrolytic bath that houses a range of chemicals suitable for the process along with properly insulated electrodes attached to a power supply source connected to a separate rectifier unit set at the correct voltage level depending on which specific type of metal needs to be deposited. Additional equipment includes filters to keep dirt particles out from entering into both tanks along with safety measures such as shields or covers over all exposed electrical components inside the tank itself.
Are there any specific precautions need when performing electo-plating?
It is important to follow all relevant safety protocols when performing electroplating especially given that this process involves hazardous materials like acids and caustic solutions which should never come into contact with skin or eyes without wearing appropriate protective gear such as gloves and eyewear when working with these substances directly. Furthermore it is important not to mix different types of chemicals together unless instructed by experienced personnel since this could potentially cause explosions when combined improperly.
Final Words:
In conclusion, Electro-Deposition (ED) is a type of metallurgic process which uses electric currents to apply thin coats of metal onto objects providing them with increased durability against wear and tear while also improving their performance in some cases by reducing their friction coefficient or increasing their electrical conductivity levels when applied with thinner coatings subjecting them to lower energy costs during application processes while still achieving reliable results leading into numerous applications possibilities within coming industry sectors which require sophisticated operations involving precise monitoring systems due solely on design parameters associated with each application scenario being performed during any given project.
ED also stands for: |
|
All stands for ED |