What does DIP mean in MILITARY
Die In Place (DIP) is a term used to describe the ability of electronic components to function and remain stationary in specific locations. Components with this ability are usually found on circuit boards or in other small, confined spaces. With DIP, the need for soldering or using mounting screws is eliminated, making electronics installation faster and easier.
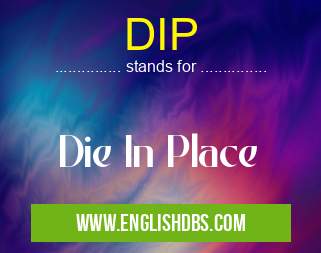
DIP meaning in Military in Governmental
DIP mostly used in an acronym Military in Category Governmental that means Die In Place
Shorthand: DIP,
Full Form: Die In Place
For more information of "Die In Place", see the section below.
» Governmental » Military
Definition
Die-In-Place is a design behavior where an IC (integrated circuit) is mounted directly onto the printed circuit board ("PCB") without the need for attaching it with additional hardware. This type of mounting allows for better heat dissipation from components and improved assembly times with fewer manual operations. Manufacturers have developed various techniques to enable DIP such as surface-mount technology, flip-chip methods, tape automated bonding and more.
Advantages
The main benefit of Die In Place is that it makes electronic assembly faster and simpler due to its easy implementation compared to traditional soldering processes. Additionally, DIP helps reduce the risk of miss alignment during assembly and improves overall product quality which can provide cost savings due to less rework or scrap materials. Other advantages include improved electrical performance due to better heat dissipation as well as shorter interconnects allowing for higher speed circuitry designs.
Essential Questions and Answers on Die In Place in "GOVERNMENTAL»MILITARY"
What is Die in Place (DIP)?
Die In Place is a practice that allows companies to test hardware prototyping and software coding on real-world conditions as part of their product development cycle. DIP tests are conducted in the environment where the final product will be used, providing opportunities for feedback from users and engineers alike.
How does Die In Place (DIP) works?
A successful DIP requires thorough planning. This includes setting up a testing area with the necessary equipment, writing automated test scripts, configuring the necessary hardware, collecting user information and setting expectations for results. After these steps are taken, the actual testing phase begins. During this phase engineers analyze data collected from the environment and adjust prototypes accordingly until they reach requirement satisfaction goals set by stakeholders.
How often should I conduct a Die In Place (DIP) test?
The frequency of DIP testing depends on the individual project requirements; some may require more frequent testing than others. Generally speaking, it's best to conduct DIP tests at regular intervals throughout the development cycle in order to ensure that no major changes have been made that could impact user experience or system performance. Additionally, regular tests can help identify potential issues early on before they become costly fixes down the line.
What kind of environments can I use for Die In Place (DIP) testing?
Generally speaking, any environment that is representative of the intended production environment can be used for DIP testing — depending on what type of product is being tested, suitable environments can range from home offices all the way up to professional production sites located around the world. Additionally, many organizations opt to use virtual environments or simulators as alternatives when physical locations are not feasible options due to geographical constraints or cost concerns.
What types of products can be tested using Die In Place (DIP)?
Any hardware or software product which needs to be tested against real-world conditions prior to launch can benefit from DIP testing. Examples could include consumer electronics such as phones or televisions; medical devices such as pacemakers or insulin pumps; industrial machinery like robotics and 3D printers; web applications like ecommerce websites; and even complex AI-driven systems with multiple components such as autonomous vehicles.
Are there any risks associated with conducting a Die In Place (DIP) test?
As with any type of experimental process there are inherent risks associated with conducting a live field trial — however most of these risks can be mitigated through proper preparation and risk management procedures prior to running a test. To minimize risks it's important to thoroughly document expected outcomes before beginning a test run so that any unexpected results can quickly be identified and addressed accordingly.
Why should I invest in a well-planned Die In Place (DIP) strategy?
Investing in proper DIP strategy pays dividends in terms of ensuring that products perform as expected out in production environments when launched - avoiding costly mistakes due to unexpected interactions between components which were not previously identified during bench or simulation tests alone. Additionally, employing a comprehensive DIP strategy helps avoid delays due to unknown bug fixes once deployed into production environments.
What type of data should I collect during my Die In Place (DIP) tests?
The type of data collected during each test varies based on specific project requirements but generally speaking core metrics such as latency times and system resources consumed should be tracked along with other relevant factors such as user input validation accuracy and customer feedback scores if available.
Final Words:
Die In Place provides electronics manufacturers with a flexible solution that accelerates assembly times while also improving product reliability. With its positive impacts on both speed and quality, DIP has become an integral part of many modern manufacturing processes used today helping manufacturers deliver their products quickly and efficiently.
DIP also stands for: |
|
All stands for DIP |