What does CTPZ mean in PLASTICS
In the world of engineering, an acronym is an abbreviation used to refer to a longer name or phrase. An acronym like CTPZ stands for Crack Tip Plastic Zone and is used in engineering to describe the area around a crack that has undergone plastic deformation. The CTPZ is an area of residual stress and strain whose size and shape are important for understanding the behavior of materials. In this article, we will delve further into what CTPZ stands for and explore its associated concepts in more detail.
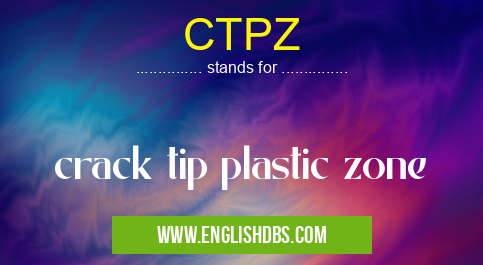
CTPZ meaning in Plastics in Miscellaneous
CTPZ mostly used in an acronym Plastics in Category Miscellaneous that means crack tip plastic zone
Shorthand: CTPZ,
Full Form: crack tip plastic zone
For more information of "crack tip plastic zone", see the section below.
Definition
CTPZ stands for “Crack Tip Plastic Zone” and describes the zone of plastic deformation surrounding a crack tip in most metals and composites. This area experiences plastic deformation when a load is applied to it, resulting in residual stress and strain. This zone also contains localized slip activity and microstructural changes that can lead to a change in material properties such as hardness, strength, fatigue life, and corrosion resistance.
How it works
The CTPZ is formed by a combination of several forces acting on the material near the crack tip including shear strain and normal stress components as well as dislocation motion. Shear strain occurs when one portion of a material is subjected to higher loads than another portion creating shear stresses at the interface which cause one side to deform while the other remains unchanged. Normal stress occurs when two materials are compressed together causing them both to deform but with different degrees of displacement measured from their original state before compression took place. Both types of stresses can result in plastic deformation along with local slip activity due to dislocations within the lattice structure that aid in relieving shear strain or normal stress during loading conditions.
Applications
The CTPZ is an important concept when studying fatigue failure mechanisms since it often indicates how efficiently a material can resist fracture under repeated loading cycles. Studies have shown that larger CTPZ dimensions result in more brittle materials with lower fatigue lives compared to those with smaller crack tip plastic zones as they are unable to adequately handle larger loads over time without fracturing or failing under excessively high stresses at lower levels than expected. Other applications include studying corrosion resistance properties since larger CTPZ sizes indicate higher rates of corrosion due to increased porosity created by plastic deformation during loading conditions.
Essential Questions and Answers on crack tip plastic zone in "MISCELLANEOUS»PLASTICS"
What is a crack tip plastic zone?
A crack tip plastic zone is an area of distorted material near the tip of a crack. It occurs when the stress field in the vicinity of the crack tip exceeds the yield stress of the material, causing it to deform plastically until the stress has decayed below this value. This region typically has an approximately triangular shape and significant internal strain, making it highly susceptible to fatigue cracking.
How is a CTTPZ formed?
A CTTPZ is generally formed as a result of cyclic loading on an existing structure containing a crack, such as during operation or maintenance activities. As each cycle of loading occurs, the stresses in the area around the crack tip will exceed its yield strength, resulting in successive cycles of plastic deformation until the stresses have been sufficiently reduced.
What materials are most susceptible to forming CTTPZs?
Most ferrous and non-ferrous metals are susceptible to forming CTTPZs due to their mechanical properties being strongly affected by cyclic loading. Polymers may also form CTTPZs under certain conditions, usually those involving repeated cycles under high temperatures or pressures.
What effects do CTTPZs have on structures?
Having a CTTPZ present can significantly increase the risks associated with fatigue cracking in structures such as aircraft components and infrastructure due to its high levels of strain concentration and susceptibility to further fatigue damage. The presence of a CTTPZ can also reduce overall structural integrity due to reduced section thickness and weakened material properties caused by plastic distortion.
Can I measure CTTPZ size without using calculations?
Yes - one method for assessing joint or component strength involves measuring both fatigue life (expected number of load cycles) and fracture toughness (resistance against propagating cracks). Both parameters are influenced by plasticity at any given location including at a crack tip, so by measuring these two values alongside other factors such as geometry, material properties and applied loads it is possible to assess potential size and shape of any defects that may be present within your construction including any potential cracking at the tips. This process gives an indication as to whether further inspection or repairs are needed before structural integrity can be assured.
Does analyzing a CTTPZ require mathematical calculations?
Yes - due to their intricate nature, performing detailed calculations around plastic zones requires knowledge in fields such as fracture mechanics; linear elastic fracture mechanics (LEFM), finite element analysis (FEA), and energy release rates (ERR). These allow for more accurate calculations around how much force needs to be applied before a defect forms within your construction and how severely it might affect overall performance if left unattended.
What can I do if I find evidence of a crack tip plastic zone within my structure?
If you discover evidence that suggests there may be structural weaknesses within your construction caused by crack tip plastic zones, then it is important that you seek out professional advice from experts in fracture mechanics who can assist you with assessing its significance and developing an appropriate course of action for repair or replacement if necessary. Depending on the context this could involve various methods such as welding operations or application of composite materials.
Is there any way I prevent formation of CTPPZs?
Yes – following protocols which help minimize stress concentrations in components avoiding sudden changes in section or excessive notch angles, ensuring correct lubrication levels etc., will usually help reduce risk associated with CTPPZ formation during operation or assembly activities. Additionally considering alternative designs which would reduce loading cycles over time may also prove beneficial.
Can CTPPZs cause problems outside normal use scenarios?
Yes – things like environmental forces e.g windload/seismic events/water ingress/temperature variation etc., which apply external forces albeit not cyclically may still cause CTPPZ formation outside expected operational usage cases.
Are there any safety measures related to controlling CTPPZ dangers?
Yes – depending on specific context protective measures should be implemented e.g corrosion prevention coatings/coatings minimising temperature fluctuations/Rust preventive oils etc., inspections should be performed at regular intervals especially after long periods between usages with particular attention paid towards ‘hot spots’ which tend see higher risk from premature failure due CTPP formations
Final Words:
In conclusion, CTRPZ stands for Crack Tip Plastic Zone which refers to the area near a crack tip that experiences plastic deformation when subjected to loads such as shear or normal intensity forces. The exact size and shape of this region has been studied extensively since it greatly affects many factors such as fatigue life and corrosion resistance which need be taken into consideration when designing structures intended for long-term use. By understanding what CTRPZ stands for engineers are able to better predict both material performance characteristics under dynamic changing circumstances such as those caused by cyclical loading over time.