What does CPACS mean in AIRCRAFT & AVIATION
CPACS is an acronym for Common Parametric Aircraft Configuration Schema. It is a data format standard utilized by the aerospace industry to store and exchange aircraft system models and their associated parameters. CPACS can simplify the sharing of digital information between multiple parties as it provides a standardized way to exchange aircraft system models used in design engineering, technology development, operation, and maintenance activities. This helps to reduce the time and cost associated with preparing tailored data sets whenever two different partners need to collaborate on a project.
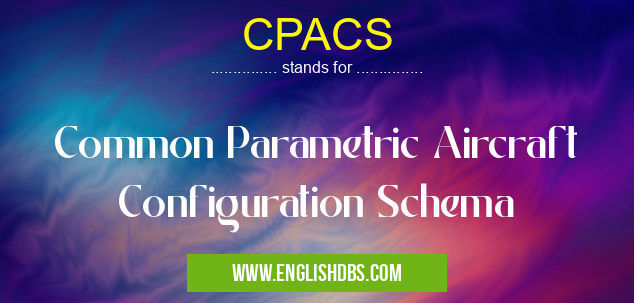
CPACS meaning in Aircraft & Aviation in Miscellaneous
CPACS mostly used in an acronym Aircraft & Aviation in Category Miscellaneous that means Common Parametric Aircraft Configuration Schema
Shorthand: CPACS,
Full Form: Common Parametric Aircraft Configuration Schema
For more information of "Common Parametric Aircraft Configuration Schema", see the section below.
Purpose
CPACS was developed by Airbus in cooperation with other airframe manufacturers, engine companies, research organizations, suppliers, and universities. The aim of this standard is to facilitate the efficient flow of consistent and accurate information throughout the entire product lifecycle from concept design to production operations; it also aims to allow companies from various fields within the industry to share data more effectively with each other. CPACS is compliant with both UAS (or unmanned) aircraft as well as manned ones so that all designs are equally supported when using this system model.
Benefits
Aircraft manufacturers can greatly benefit from CPACS standardization due to its ability to save time and money throughout all stages of product development. With consistent models being exchanged among diverse teams there’s less effort required for managing various versions of different partner’s experiments during the certification phase or any other stage within product’s life cycle; resulting in improved quality assurance through common validation standards over many platforms. Furthermore, engineers who are current users of this technology have reported better workflows due in part to its user-friendly graphical interface which allows them access a wide range of 3D visualizations including detailed images of wireframes or rendering perspectives for quick understanding at any stage when examining structural issues that may arise in deep analysis scenarios.
Essential Questions and Answers on Common Parametric Aircraft Configuration Schema in "MISCELLANEOUS»AIRCRAFT"
What is CPACS?
CPACS (Common Parametric Aircraft Configuration Schema) is a standardized XML format for describing an aircraft's configuration and performance characteristics. It was developed by the OpenMDAO initiative as part of the Airbus AIM project and is now maintained as an open source project under the LGPL license. It provides a consistent, platform-independent method of representing aircraft data to facilitate aircraft design exploration and comparison.
Is CPACS an open source project?
Yes, it has been released under the LGPL license and is maintained as an open source project.
Who maintains CPACS?
The OpenMDAO initiative maintains CPACS as part of their Airbus AIM project.
What are some advantages of using CPACS?
The main advantage is that it provides a consistent, platform-independent method of representing aircraft data to facilitate aircraft design exploration and comparison. Additionally, it reduces cost and complexity in the development process because it eliminates manually entering data in multiple formats into different applications.
Is there any software that supports CPACS files?
Yes, many CAD/CAM applications such as Catia, Matlab/Simulink and Aerospace Toolbox support reading and writing CPACS files. There are also tools specifically designed for editing or visualizing CPACS files such as CASe Editor or XRLab Studio.
What type of aircraft data does CPACS represent?
It represents all aspects of an aircraft structure including geometry information (wings, fuselage etc.), loading conditions (static loadings, gusts etc.), flight loading conditions (variation in lift coefficient with speed etc.) aerodynamic coefficients (drag polar etc.), propulsion system details (engine model, reaction heights etc.) control surface position limits etc., mass and inertia properties.
DoesCPacsallow simulation analysis?
Yes, it allows simulation analysis by providing models for structural dynamics simulations such as eigenmodes calculations or flutter analyses which allow engineers to predict needed structural reinforcements before manufacture begins.
How can I get started with using CPACS? A: To get started you will need access to the necessary software to create or read a CPACs file - typically either a CAD application or one specializing in editing or visualizing files within this format such as CASe Editor or XRLab Studio. You should then familiarise yourself with the XML notation used within this format to enable you to edit existing files correctly or create new ones from scratch. Once you have created your file you should run verification tests against it using validation tools provided on theOpenMDAO website before using for simulations/analysis purposes.[END] Q: How do Ivalidate myCPacsfile?
To get started you will need access to the necessary software to create or read a CPACs file - typically either a CAD application or one specializing in editing or visualizing files within this format such as CASe Editor or XRLab Studio. You should then familiarise yourself with the XML notation used within this format to enable you to edit existing files correctly or create new ones from scratch. Once you have created your file you should run verification tests against it using validation tools provided on theOpenMDAO website before using for simulations/analysis purposes.
Final Words:
In conclusion, CPACS is an important tool for improving collaboration between multiple partners in the aerospace industry while keeping detailed records on complex systems throughout their product life cycles – thanks largely in part due its use of standardized methods which make data exchange easier than ever before! This ensures that projects remain manageable even when dealing with diverse teams who are working together over long periods of time; helping stakeholders save both money and energy while still producing high-quality products for customers around the world!