What does COPQ mean in GENERAL
COPQ is an acronym for Cost of Poor Quality, which in business is the cost incurred due to providing products or services with inadequate quality. Poor quality can be defined as having features that do not meet customer expectations or requirements. COPQ is often used as a measure of success when assessing the impact of quality improvements initiatives, and it provides an all-encompassing view of the overall costs related to poor product quality.
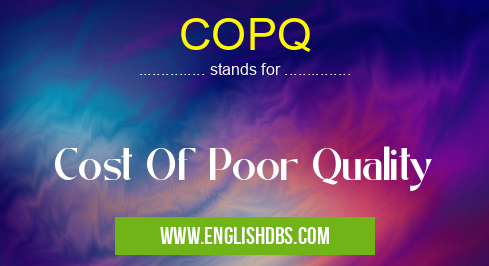
COPQ meaning in General in Business
COPQ mostly used in an acronym General in Category Business that means Cost Of Poor Quality
Shorthand: COPQ,
Full Form: Cost Of Poor Quality
For more information of "Cost Of Poor Quality", see the section below.
What it means
COPQ describes all the dollars spent dealing with poor quality in a company's products or services. This includes losses from returns, reworking, warranties, failed inspections and repairs, scrap, non-conformities and other costs related to below par performance. It can also include indirect factors such as brand damage caused by negative online reviews and decreased customer loyalty due to substandard output from a particular product or service. Companies need to understand how these costs contribute to their bottom line if they want to minimize them and maximize profits.
What it is used for
COPQ is increasingly being used by businesses in order to measure their success in improving product quality and reduce waste resulting from defects. Businesses are able to quantify the financial impact of poor quality through estimating COPQ and comparing these figures over time, allowing them to track progress in improving product/service performance. It also helps companies identify areas where quality needs improvement so that resources can be directed towards fixing those problems first. This information can then be used when devising strategies for improvement initiatives.
Essential Questions and Answers on Cost Of Poor Quality in "BUSINESS»GENERALBUS"
What is COPQ?
COPQ stands for Cost of Poor Quality, which involves the expenses incurred from problems that arise due to poor quality processes, inefficiencies or errors. These costs can be direct or indirect and include costs associated with scrap, rework, extra material and labor, lost sales, warranty claims, customer returns, warranties and recalls.
What are some common examples of COPQ?
Common examples of COPQ include the cost to repair product defects; the cost to resolve customer complaints or grievances; the cost for failed inspections; the cost of downgrading products; and any other costs associated with producing a defective product.
How can a company measure its COPQ?
Companies can measure their COPQ by calculating the total amount spent on repairing defects and resolving customer complaints and grievances over a certain period of time. This can help identify if there are any areas where efforts need to be focused to reduce these costs. Additionally companies may use benchmarking techniques to compare their performance against others in the same industry.
How can companies reduce their COPQ?
Companies can reduce their COPQ by implementing preventive measures such as following process standardization and automation in manufacturing processes; establishing rigorous supplier selection criteria; conducting extensive market research before launching new products; implementing advanced quality control methods; minimizing scrap material production; hiring well-trained staff; carrying out regular audits of all processes; providing continuous employee training programs etc.
What are some best practices for managing COPQ?
Some best practices for managing COPQ include setting up measurable goals for reducing overall quality costs; creating a culture within the organization that encourages proactive problem solving activities that address root causes instead of solely focusing on eliminating symptoms (symptom management); tracking key metrics related to quality control such as defect rate and cycle time ; using industrywide benchmarks as reference points when assessing performance and making improvements etc.
What are the benefits of reducing COPQ?
The benefits of reducing COOPQ include increased customer satisfaction and loyalty as well as improved organizational efficiency through reduced waste materials or production downtime due to faulty components or error-ridden figures. Furthermore, improved quality standards also help save money through lower insurance premiums due to fewer product recall requirements. Moreover, it also promotes brand recognition for businesses yielding better returns in terms of sales figures.
Why is it important to have an effective strategy for tackling COPR?
It is important to have an effective strategy for tackling COOB because it helps organizations identify weak links within their value chain operations while ensuring timely corrective actions are taken that lead to efficient implementations leading towards reduced expenses in form of fewer woes related with production setbacks resulting from poor quality measurements.
What should a good strategy for managing Copq involve?
A good strategy for managing Copq should involve establishing clear objectives relatedto costs reduction via ongoing improvement initiatives across all business units or departments involved in manufacturing processes accompanied with incorporating improvement plans into day-to-day operational functions together with monitoring key targets like rework percentages or numbers related with customer concerns.
Final Words:
In conclusion, COPQ stands for Cost Of Poor Quality and is a metric used by businesses in order to assess the financial impact of providing inadequate products/services on their bottom line. This valuable information allows companies to identify areas where improvement initiatives are needed in order to reduce costs associated with waste resulting from defects or substandard output of a particular product/service. Understanding COPQ enables organizations to become more efficient and maximize profits while creating higher customer satisfaction levels.