What does CMRM mean in MANAGEMENT
CMRM stands for Chemical and Material Risk Management, which is a process of managing chemicals and materials in a safe and sustainable way. CMRM seeks to identify and control potential risks to people, the environment, and property. It involves the identification, evaluation, monitoring, communication, and management of hazardous chemicals or materials used in production processes or operations. CMRM focuses on reducing risk by preventing chemical or material releases into the environment.
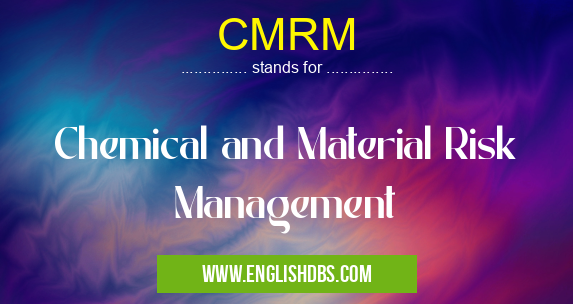
CMRM meaning in Management in Business
CMRM mostly used in an acronym Management in Category Business that means Chemical and Material Risk Management
Shorthand: CMRM,
Full Form: Chemical and Material Risk Management
For more information of "Chemical and Material Risk Management", see the section below.
» Business » Management
Essential Questions and Answers on Chemical and Material Risk Management in "BUSINESS»MANAGEMENT"
What is Chemical and Material Risk Management?
Chemical and Material Risk Management (CMRM) is a process of managing chemicals and materials in a safe and sustainable way. It seeks to identify and control potential risks to people, the environment, and property by preventing chemical or material releases into the environment.
What are some goals of CMRM?
The primary goals of CMRM include reducing risk by identifying hazards associated with chemical substances or materials used in production processes or operations; evaluating existing management systems; monitoring exposures; developing preventative controls; communicating hazard information to workers; providing training on proper handling procedures; implementing management strategies; monitoring chemical levels; establishing contingency plans; evaluating compliance with relevant laws and regulations; maintaining record-keeping systems; continually assessing safety performance; and responding quickly to incidents involving hazardous chemical substances or materials.
How often should CMRM be conducted?
The frequency of CMRM will depend on many factors such as the type of business operation, complexity of the system being managed, level of risk associated with particular activities involved in the operation etc. Generally speaking, assessments should be conducted at least once every three years but can be conducted more frequently if needed due to changing conditions or new hazards being introduced.
Who is responsible for implementing CMRM?
The responsibility for implementing CMRM lies with company managers at all levels who have direct knowledge of processes that use potentially hazardous chemicals or materials. Additionally, external certified professionals may also be consulted for advice on specific aspects related to the implementation of CMRM activities within an organization.
What are some common challenges associated with CMRM?
Common challenges associated with implementing effective CMRM include incomplete hazard assessment data due to inadequate sampling methods employed during risk assessments as well as lack of resources dedicated to necessary training related to safe handling procedures for employees working with potentially hazardous chemicals or materials. Additionally poor communication between various departments involved in overseeing safety practices can cause delays in responding quickly to incidents involving hazardous substances or materials thereby increasing vulnerability. Lastly difficulties in convincing staff members about importance of stringent safety protocols can also limit successful implementation of robust Chemical & Material Risk Management Practices.
Final Words:
Effective implementation of Chemical & Material Risk Management practices can help protect people from exposure to dangerous chemicals & materials used in production process & operations resulting in heightened safety standards & improved public health outcomes across industries.