What does LHG mean in UNCLASSIFIED
LHG is an abbreviation that stands for Lapping, Honing, Grinding. These are three distinct processes used in manufacturing to achieve specific surface finishes on metal components. Each process has its own unique characteristics and applications.
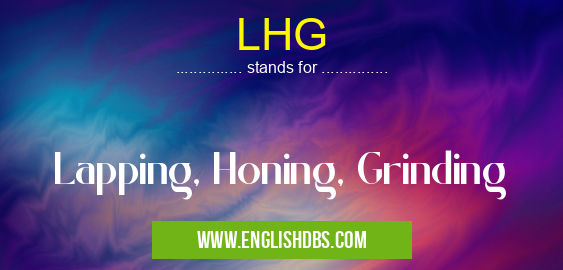
LHG meaning in Unclassified in Miscellaneous
LHG mostly used in an acronym Unclassified in Category Miscellaneous that means Lapping, Honing, Grinding
Shorthand: LHG,
Full Form: Lapping, Honing, Grinding
For more information of "Lapping, Honing, Grinding", see the section below.
Lapping
Lapping is a process that involves abrading a surface using a fine abrasive slurry and a lap, which is a flat or contoured surface made of a soft material. The lap is moved back and forth across the surface, removing material and creating a smooth, polished finish. Lapping is often used to finish precision components, such as optical lenses and bearings.
Honing
Honing is a process that uses an abrasive stone to remove material from the bore of a cylindrical component. The stone is rotated and reciprocated within the bore, creating a smooth, accurate surface. Honing is often used to finish the bores of engines, hydraulic cylinders, and other precision components.
Grinding
Grinding is a process that uses an abrasive wheel to remove material from a surface. The wheel is rotated at high speed and brought into contact with the surface, removing material and creating a smooth, consistent finish. Grinding is used to finish a wide variety of components, from small cutting tools to large castings.
Essential Questions and Answers on Lapping, Honing, Grinding in "MISCELLANEOUS»UNFILED"
What is lapping, honing, and grinding (LHG)?
LHG refers to a group of abrasive machining processes used to finish metal surfaces. Lapping involves fine abrasives on a rotating lap to remove material and create a smooth, flat surface. Honing uses a rotating tool with abrasive stones to bore and finish cylindrical surfaces. Grinding uses abrasive grinding wheels to remove material and shape workpieces.
What are the advantages of LHG?
LHG provides high precision and surface finish, reducing friction and wear. It improves dimensional accuracy, surface quality, and functional performance of components. LHG processes are versatile and can be applied to a wide range of materials.
What is the difference between lapping, honing, and grinding?
Lapping removes small amounts of material to achieve high surface finish. Honing is used for precision boring and finishing cylindrical surfaces. Grinding is a more aggressive process used to remove larger amounts of material and shape workpieces.
What are the applications of LHG?
LHG is widely used in various industries, including aerospace, automotive, medical, and manufacturing. It is employed in applications such as finishing optical lenses, precision bore sizing, and grinding cutting tools.
What factors affect the quality of LHG?
The quality of LHG depends on several factors, including abrasive selection, tool geometry, process parameters, and surface preparation. Proper selection and optimization of these factors ensure efficient and high-quality surface finishing.
What are the limitations of LHG?
LHG processes can be time-consuming and require specialized equipment and skilled operators. They are generally not suitable for large-scale production or for finishing complex geometries.
Final Words: Lapping, Honing, Grinding (LHG) are essential processes in manufacturing, used to achieve specific surface finishes on metal components. Each process has its own unique characteristics and applications, and together they play a vital role in the production of high-quality precision components.