What does KPE mean in UNCLASSIFIED
Key Process Equipment (KPE) refers to critical equipment that plays a vital role in the production process of a manufacturing facility. KPE is essential for the efficient operation and overall success of the facility.
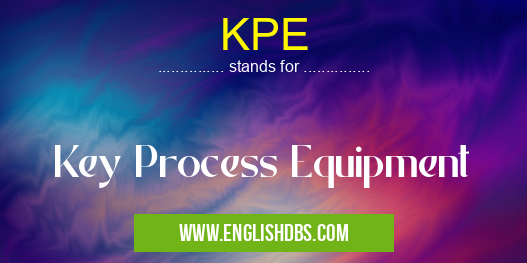
KPE meaning in Unclassified in Miscellaneous
KPE mostly used in an acronym Unclassified in Category Miscellaneous that means Key Process Equipment
Shorthand: KPE,
Full Form: Key Process Equipment
For more information of "Key Process Equipment", see the section below.
Understanding KPE
KPE typically includes equipment such as:
- Production machinery: Essential for manufacturing products, such as assembly lines, CNC machines, and robots.
- Control systems: Monitor and regulate production processes, including programmable logic controllers (PLCs), distributed control systems (DCSs), and supervisory control and data acquisition (SCADA) systems.
- Utility systems: Provide essential services, such as electricity, water, and compressed air, to support production operations.
Significance of KPE
- Product quality: KPE ensures consistent product quality by maintaining precise operating conditions.
- Production efficiency: KPE optimizes production processes, reducing downtime and increasing output.
- Safety and reliability: KPE is designed with safety features to minimize risks and ensure reliable operation.
- Cost-effectiveness: KPE can help reduce production costs by optimizing resource utilization and minimizing maintenance expenses.
Essential Questions and Answers on Key Process Equipment in "MISCELLANEOUS»UNFILED"
What is Key Process Equipment (KPE)?
Key Process Equipment (KPE) refers to the machines, systems, or devices that play a crucial role in manufacturing or processing operations. These assets are essential for achieving desired product quality, production efficiency, and compliance with regulatory standards. KPEs are typically high-value investments that require specialized maintenance and operational expertise.
How are KPEs identified?
KPEs are typically identified through a risk assessment process that evaluates the impact of equipment failure or malfunction on overall production, product quality, and safety. Factors considered include equipment complexity, maintenance history, criticality to the manufacturing process, and potential consequences of downtime.
What types of equipment are considered KPEs?
KPEs vary across industries and manufacturing processes. Some common examples include:
- Production machinery (e.g., assembly lines, injection molding machines, CNC equipment)
- Process control systems (e.g., PLCs, DCSs, MES)
- Utility infrastructure (e.g., boilers, compressors, chillers)
- Material handling equipment (e.g., conveyors, cranes, forklifts)
Why is KPE management important?
Effective KPE management is crucial for several reasons:
- Minimizing downtime and production losses: Proper maintenance and optimization of KPEs reduce the risk of equipment failures and unplanned downtime, ensuring uninterrupted production.
- Maintaining product quality: KPEs play a significant role in ensuring consistent product quality by controlling process parameters and eliminating defects.
- Ensuring regulatory compliance: KPEs often require specific maintenance and operational procedures to meet regulatory standards for safety, environmental protection, and product quality.
- Optimizing production efficiency: Regular monitoring and data analysis of KPEs allow for process improvements, capacity optimization, and reduced operating costs.
What are common challenges in KPE management?
Common challenges in KPE management include:
- Equipment obsolescence: Advancements in technology can lead to KPEs becoming obsolete, requiring upgrades or replacements to maintain production capabilities.
- Maintenance and repair costs: KPEs often require specialized maintenance and repairs, which can be costly and time-consuming.
- Skills shortage: Ensuring a qualified workforce with the expertise to maintain and operate KPEs can be challenging in some industries.
- Data management and analytics: Collecting and analyzing data from KPEs can be complex, but essential for optimizing performance and predicting maintenance needs.
Final Words: KPE is a crucial element in manufacturing operations. By understanding its significance and optimizing its performance, manufacturers can enhance their production capabilities, ensure product quality, and achieve overall business success.
KPE also stands for: |
|
All stands for KPE |