What does QAL mean in QUALITY ASSURANCE & CONTROL
Quality Assurance List (QAL) is a set of rules, regulations, and criteria for the quality of products or services which are expected to be provided. It serves as a benchmark for the performance of these products or services and ensures that they meet established standards. Quality assurance consists of monitoring and evaluating processes to ensure that it meets the requirements. It is an important aspect in the delivery of any product or service and helps to maintain customer satisfaction.
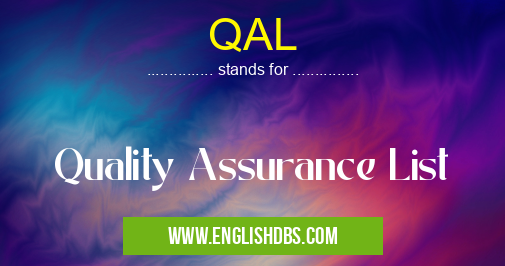
QAL meaning in Quality Assurance & Control in Miscellaneous
QAL mostly used in an acronym Quality Assurance & Control in Category Miscellaneous that means Quality Assurance List
Shorthand: QAL,
Full Form: Quality Assurance List
For more information of "Quality Assurance List", see the section below.
Benefits of Using QAL
Using QAL can help organizations improve their overall efficiency, reduce costs associated with production or delivery, and maintain customer satisfaction by providing a consistent level of quality across all products and services. Having an up-to-date QAL also helps ensure compliance with applicable laws and regulations while still maintaining cost savings. Additionally, having this standard in place can cut down on the time spent troubleshooting problems related to quality since consistent expectations are already outlined in the document.
Essential Questions and Answers on Quality Assurance List in "MISCELLANEOUS»QUALITY"
What is a QAL?
A Quality Assurance List (QAL) is a comprehensive report that covers both quality and technical compliance matters for a particular product or service. It outlines the requirements for quality control, assesses the performance of your product or service, identifies possible risks and provides solutions to ensure that those risks are managed appropriately.
How is QAL used?
QALs are used in various industries such as manufacturing, engineering, medical device manufacturing and software development. They offer a systematic way of assessing the performance of products and services, helping to identify potential issues before they become serious problems. QALs also provide an effective method of tracking changes over time and ensuring that all aspects of quality assurance remain compliant with regulatory standards.
Who develops a QAL?
A Quality Assurance List (QAL) is typically developed by an engineer or quality assurance manager who is familiar with the regulations governing the industry-specific product or service being assessed. This person will work with other departments to develop requirements for evaluation and make sure they meet applicable standards.
What should be included in a QAL?
A good Quality Assurance List should include details about the procedures used to evaluate the product/service; requirements for documentation; instructions for testing; data collection protocols; definitions of key terms; any applicable regulations; corrective action plans; audit schedules; reports detailing results; and a clear set of rules regarding handling non-compliance issues.
How often should a QAL be updated?
The frequency at which you update your Quality Assurance List depends on several factors including the complexity of the product/service being evaluated, the industry in which it operates, changes to relevant regulations, and advances in technology. In most cases, it's best practice to review your QAL at least annually - or more frequently depending on specific circumstances - to make sure it reflects current trends and remains compliant with all relevant standards.
What data should be collected for QAL?
The exact data you collect depends on your industry and specific needs but may include things like test results from prototypes or finished products, customer feedback surveys, complaints records, design schematics or diagrams, production information such as production date batch numbers etc., supplier records, performance figures related to energy use etc., technical documents such as installation manuals etc., inspection documents outlining any discrepancies discovered during inspections etc., calibration records etc., process validation documents etc., certification reports etc., risk analysis documents outlining any risk management measures taken during production etc.
How can I ensure my product meets my internal standard when using QAL?
To ensure that your product meets all internal standards when using the Quality Assurance List (QAL), you should continuously monitor current trends in both technology and regulations related to your industry sector. Your team should also take regular reviews of both completed projects as well as ongoing projects - this will help identify any discrepancies between what was expected/planned compared to what happened during completion/execution stages so that corrective measures can be taken quickly if necessary. Additionally, don't forget to document all evaluations thoroughly so you have evidence if needed later on.
Who carries out regular audits when using a QAL?
To ensure compliance with regulatory standards is maintained while using Quality Assurance Lists (QALS), regular audits need to be conducted by an independent third party auditing company. This company will review all documentation relating to evaluations conducted and follow up with their own evaluations where necessary before providing their report detailing findings - this helps provide complete transparency about how compliant operations are throughout all areas associated with production.
What happens if non-compliance issues arise when using a QAL?
If non-compliance issues arise while using Quality Assurance Lists (QALS), then it's important that these are addressed immediately rather than waiting until later down the line when costs may have escalated due to taking no corrective action earlier on in proceedings. The first step would usually involve performing investigations into what caused these issues so that proper steps can be taken towards rectifying them.
Final Words:
Quality assurance lists are essential tools for any organization that wants to remain competitive in their industry without sacrificing quality. By ensuring all aspects related to production or delivery are specified ahead of time, organizations can save money by avoiding costly mistakes as well as increase customer satisfaction by offering consistently high-quality products and services over time.
QAL also stands for: |
|
All stands for QAL |