What does DYMAC mean in SOFTWARE
DYMAC, short for DYnamic MAterial Control, is a comprehensive inventory management system designed to streamline and optimize the control of materials within an organization. It offers a range of features that enable businesses to effectively track, manage, and optimize their inventory levels, reducing waste and improving operational efficiency.
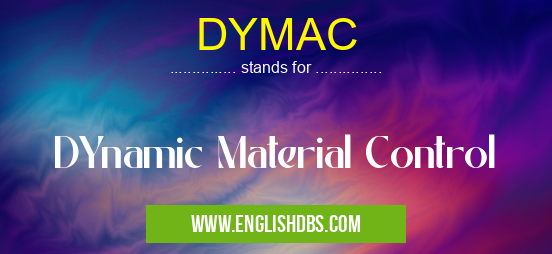
DYMAC meaning in Software in Computing
DYMAC mostly used in an acronym Software in Category Computing that means DYnamic Material Control
Shorthand: DYMAC,
Full Form: DYnamic Material Control
For more information of "DYnamic Material Control", see the section below.
Key Features of DYMAC
- Inventory Tracking: DYMAC provides real-time visibility into inventory levels across multiple locations, including warehouses, distribution centers, and retail stores. It enables businesses to track inventory movements, including receipts, shipments, and adjustments, ensuring accurate and up-to-date stock information.
- Material Management: DYMAC facilitates efficient material management by providing tools for classifying, categorizing, and organizing items based on their properties, attributes, and usage. It helps businesses optimize storage space, reduce redundancy, and improve material flow.
- Demand Forecasting: DYMAC incorporates demand forecasting capabilities that leverage historical data, trend analysis, and market intelligence to predict future demand for materials. This enables businesses to proactively adjust inventory levels, minimize stockouts, and prevent overstocking.
- Order Management: The system integrates with order processing systems to automate order fulfillment, ensuring efficient and timely delivery of materials to customers. It manages backorders, tracks order status, and provides real-time updates on order progress.
- Replenishment Planning: DYMAC optimizes inventory replenishment by analyzing demand patterns, lead times, and safety stock levels. It generates replenishment orders based on predefined rules and parameters, ensuring that materials are available when needed while minimizing carrying costs.
Benefits of Using DYMAC
- Improved Inventory Control: DYMAC provides greater visibility and control over inventory, reducing the risk of stockouts, overstocking, and waste.
- Optimized Material Management: Efficient material management practices reduce storage costs, streamline material flow, and improve operational efficiency.
- Accurate Forecasting: Demand forecasting capabilities help businesses anticipate demand and adjust inventory levels accordingly, minimizing disruptions and improving customer satisfaction.
- Efficient Order Fulfillment: Seamless integration with order processing systems ensures timely and accurate order fulfillment, reducing delivery delays and improving customer experience.
- Lower Inventory Costs: Optimized replenishment planning helps businesses reduce inventory carrying costs while ensuring that materials are available when needed.
Essential Questions and Answers on DYnamic Material Control in "COMPUTING»SOFTWARE"
What is DYMAC (DYnamic Material Control)?
DYMAC is a software solution that provides real-time visibility and control over materials used in manufacturing processes. It helps organizations optimize material usage, reduce waste, and improve overall efficiency.
How does DYMAC work?
DYMAC uses a combination of sensors, software, and data analytics to track material usage and inventory levels. It integrates with enterprise resource planning (ERP) systems to provide a comprehensive view of material flow throughout the manufacturing process.
What are the benefits of using DYMAC?
DYMAC offers numerous benefits, including:
- Reduced material waste
- Improved inventory management
- Increased production efficiency
- Enhanced traceability and compliance
- Real-time visibility into material consumption
What types of materials can DYMAC track?
DYMAC can track a wide range of materials used in manufacturing, including:
- Raw materials
- Components
- Work-in-progress inventory
- Finished goods
How does DYMAC improve material usage efficiency?
DYMAC provides real-time insights into material consumption patterns. This data enables manufacturers to identify areas of waste and inefficiencies, such as overstocking, understocking, and excessive scrap. By optimizing material usage, organizations can reduce costs and improve profitability.
Final Words: DYMAC is a powerful inventory management system that provides businesses with the tools and capabilities to effectively track, manage, and optimize their material resources. By integrating real-time inventory tracking, material management, demand forecasting, order management, and replenishment planning, DYMAC empowers organizations to streamline operations, reduce costs, and improve customer satisfaction through efficient inventory control.