What does SOAL mean in ASSEMBLY
SOAL stands for Sequencing Operations for Assembly Lines. It is a technique used in manufacturing to determine the optimal sequence of operations for assembling a product on an assembly line. The goal of SOAL is to minimize the total assembly time and improve the efficiency of the assembly process.
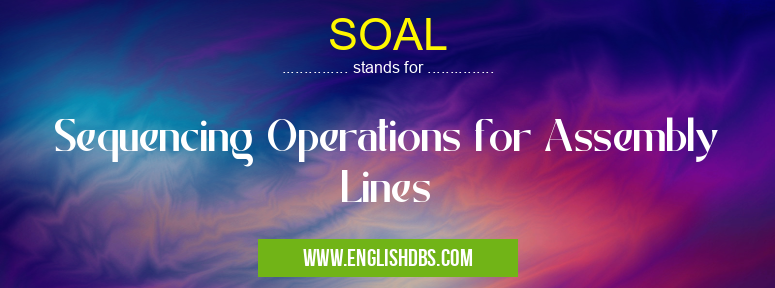
SOAL meaning in Assembly in Computing
SOAL mostly used in an acronym Assembly in Category Computing that means Sequencing Operations for Assembly Lines
Shorthand: SOAL,
Full Form: Sequencing Operations for Assembly Lines
For more information of "Sequencing Operations for Assembly Lines", see the section below.
How SOAL Works
SOAL involves the following steps:
- Product Analysis: Identifying the assembly sequence of the product, including the components, subassemblies, and the order in which they are assembled.
- Time Estimation: Determining the time required to complete each assembly operation.
- Precedence Relationships: Establishing relationships between operations that must be performed in a specific order.
- Sequencing: Developing a sequence of operations that minimizes the total assembly time, considering precedence relationships and time estimates.
Benefits of SOAL
- Reduced Assembly Time: SOAL helps identify the shortest assembly sequence, reducing the overall time required to assemble the product.
- Improved Efficiency: By optimizing the sequence of operations, SOAL eliminates unnecessary delays and bottlenecks, improving the efficiency of the assembly line.
- Reduced Costs: By minimizing assembly time and improving efficiency, SOAL can lead to significant cost savings in manufacturing.
- Increased Productivity: An optimized assembly line can produce more units per hour, increasing productivity and meeting customer demand more efficiently.
Essential Questions and Answers on Sequencing Operations for Assembly Lines in "COMPUTING»ASSEMBLY"
What is the purpose of sequencing operations for assembly lines?
Sequencing operations for assembly lines involves organizing and arranging the order of operations to create a smooth and efficient production process. By optimizing the sequence, manufacturers can minimize bottlenecks, reduce production time, and improve overall productivity.
How can sequencing operations improve assembly line efficiency?
Proper sequencing can lead to several benefits, including:
- Reduced workstation idle time by ensuring a steady flow of work
- Improved ergonomics and reduced operator fatigue by optimizing the sequence of movements
- Minimized inventory requirements by reducing work-in-process
- Increased productivity by optimizing the use of resources and reducing production time
What factors should be considered when sequencing assembly line operations?
When sequencing operations, it is crucial to account for various factors, such as:
- Precedence constraints: Identifying the operations that must be completed before others
- Workstation capacity: Determining the capabilities and limitations of each workstation
- Material flow: Ensuring a smooth and efficient flow of materials throughout the assembly line
- Operator skills: Matching the operations to the skill level of the operators
What techniques are commonly used for sequencing assembly line operations?
Several techniques can be employed for sequencing operations, including:
- Activity precedence diagramming: Creating a graphical representation of the precedence relationships between operations
- Line balancing: Dividing the assembly line into workstations with roughly equal workloads
- Heuristic methods: Using rules or guidelines to generate a sequence
What are the challenges associated with sequencing assembly line operations?
There are a few challenges that arise in sequencing assembly line operations:
- Complexity: Determining the optimal sequence can be complex, especially for lines with multiple products or operations
- Changes: Production changes or new product introductions can require adjustments to the sequencing
- Balancing: Achieving a balanced line that minimizes bottlenecks and idle time can be challenging
Final Words: SOAL is a valuable technique in manufacturing that helps optimize assembly line operations. It provides a structured approach for determining the most efficient sequence of operations, leading to reduced assembly time, improved efficiency, and increased productivity. By implementing SOAL, manufacturers can streamline their assembly processes and achieve significant benefits in terms of cost, time, and quality.
SOAL also stands for: |
|
All stands for SOAL |