What does MCS mean in UNCLASSIFIED
MCS (Machine Coordinate System) is a coordinate system used to define the position and orientation of a tool or workpiece in relation to a machine tool. It is an essential part of computer-aided manufacturing (CAM) and is used to program and control the movement of machine tools such as CNC mills, lathes, and robots.
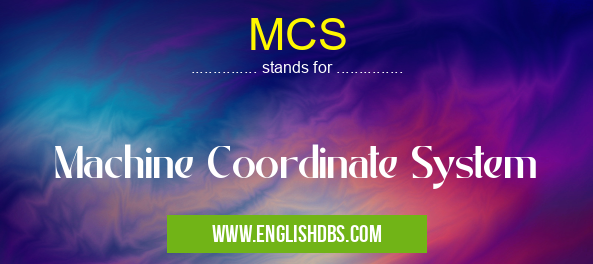
MCS meaning in Unclassified in Miscellaneous
MCS mostly used in an acronym Unclassified in Category Miscellaneous that means Machine Coordinate System
Shorthand: MCS,
Full Form: Machine Coordinate System
For more information of "Machine Coordinate System", see the section below.
Definition
The MCS is a right-handed coordinate system that defines three primary axes:
- X-axis: Horizontal axis parallel to the machine bed.
- Y-axis: Vertical axis perpendicular to the machine bed.
- Z-axis: Longitudinal axis parallel to the spindle.
The MCS is typically defined with respect to the machine tool's reference point, which is usually located at the center of the machine's work envelope. The origin of the MCS is the point where the three primary axes intersect.
Importance of MCS
The MCS is essential for accurate and efficient machining. It allows the machine tool to determine the exact position and orientation of the tool and workpiece, which is critical for achieving precise cuts and avoiding collisions. The MCS also enables the use of CAM software to generate toolpaths that optimize the machining process.
Essential Questions and Answers on Machine Coordinate System in "MISCELLANEOUS»UNFILED"
What is the Machine Coordinate System (MCS)?
The Machine Coordinate System (MCS) is a coordinate system used to define the position of points and objects within a machine, such as a CNC machine or a 3D printer. It allows for precise control of the machine's movements and the positioning of its tools.
What are the axes of the MCS?
The MCS typically uses three axes:
- X-axis: Horizontal axis running from left to right
- Y-axis: Vertical axis running from bottom to top
- Z-axis: Depth axis running towards or away from the observer
These axes form a right-handed coordinate system.
How is the MCS used in CNC programming?
In CNC programming, the MCS is used to define the path that the machine's cutting tool will follow. The programmer creates a program that contains coordinates for the tool's movements along each axis. The machine's controller then interprets these coordinates and moves the tool accordingly.
What is the difference between the MCS and the workpiece coordinate system (WCS)?
The MCS is fixed to the machine, while the WCS is attached to the workpiece. The WCS allows the programmer to specify the position and orientation of the workpiece relative to the machine. By using the WCS, the programmer can ensure that the tool is positioned correctly for machining operations.
How do I set the MCS in my CNC machine?
The method for setting the MCS varies depending on the specific machine model. Generally, it involves using the machine's control panel to define the home position and the offset from that position for each axis.
Final Words: The MCS is a fundamental concept in computer-aided manufacturing. It provides a common reference frame for defining the position and orientation of tools and workpieces in relation to machine tools. By understanding the MCS, manufacturers can program and control their machines more effectively, resulting in improved accuracy, efficiency, and productivity.
MCS also stands for: |
|
All stands for MCS |