What does QPM mean in MANAGEMENT
QPM (Quality and Production Management) is a comprehensive approach to managing and improving the quality of products or services while optimizing production processes. It encompasses a wide range of principles, practices, and methodologies to ensure that organizations consistently deliver high-quality products or services while maximizing efficiency and productivity.
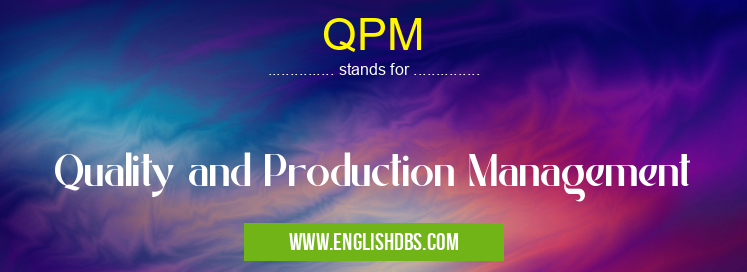
QPM meaning in Management in Business
QPM mostly used in an acronym Management in Category Business that means Quality and Production Management
Shorthand: QPM,
Full Form: Quality and Production Management
For more information of "Quality and Production Management", see the section below.
» Business » Management
### Key Elements of QPM:
- Quality Control: Establishing and implementing standards, inspections, and testing procedures to ensure products or services meet predefined quality specifications.
- Process Improvement: Continuously evaluating and optimizing production processes to reduce defects, increase efficiency, and lower costs.
- Statistical Analysis: Using statistical techniques to analyze data, identify trends, and make informed decisions regarding quality and production.
- Customer Feedback: Gathering and incorporating customer feedback to improve products or services, identify areas for improvement, and enhance customer satisfaction.
- Employee Involvement: Empowering employees and involving them in quality and production management initiatives to foster a culture of continuous improvement.
- Continuous Learning: Promoting a culture of continuous learning and development to keep up with best practices and industry trends in quality and production management.
### Benefits of QPM:
- Improved Product or Service Quality: QPM helps organizations consistently deliver high-quality products or services that meet customer expectations.
- Increased Production Efficiency: By optimizing production processes, QPM reduces waste, defects, and rework, leading to increased efficiency and productivity.
- Reduced Costs: Improved quality and efficiency translate into reduced costs associated with defects, rework, and customer complaints.
- Enhanced Customer Satisfaction: By providing high-quality products or services, QPM helps organizations build strong customer relationships and increase customer satisfaction.
- Competitive Advantage: Organizations that effectively implement QPM gain a competitive advantage by consistently delivering superior quality products or services.
### Conclusion:
QPM is an essential approach for organizations looking to improve their overall performance and achieve operational excellence. By implementing QPM principles and practices, businesses can enhance quality, increase production efficiency, reduce costs, and ultimately gain a competitive advantage in the marketplace.
Essential Questions and Answers on Quality and Production Management in "BUSINESS»MANAGEMENT"
What is Quality and Production Management (QPM)?
QPM is a comprehensive approach to improving the quality and efficiency of production processes. It involves managing all aspects of the production process, from product design and development to production planning and execution, to ensure that products meet customer requirements and are produced efficiently.
What are the benefits of implementing QPM?
Implementing QPM can provide several benefits, including:
- Enhanced product quality, leading to increased customer satisfaction and reduced warranty costs.
- Improved production efficiency, resulting in reduced waste, increased output, and lower production costs.
- Streamlined production processes, reducing lead times and improving response to changing market demands.
- Improved compliance with regulatory standards, ensuring legal adherence and mitigating risks.
What is the role of data in QPM?
Data plays a crucial role in QPM. By collecting and analyzing data, manufacturers can identify areas for improvement, monitor production performance, and make informed decisions. Data can be used to track key performance indicators (KPIs), identify trends, and predict potential issues.
How can technology support QPM?
Technology can significantly enhance QPM efforts. Enterprise resource planning (ERP) systems can provide a centralized platform for managing production processes, while quality management software can facilitate data collection, analysis, and reporting. Automation technologies, such as robotic process automation (RPA), can streamline tasks and improve efficiency.
What are some best practices for QPM implementation?
Best practices for QPM implementation include:
- Engaging all stakeholders, including employees, suppliers, and customers.
- Establishing clear quality and production goals.
- Implementing a standardized and documented QPM system.
- Providing ongoing training and support to employees.
- Continuously monitoring and evaluating QPM performance and making adjustments as needed.
QPM also stands for: |
|
All stands for QPM |