What does PFMEA mean in UNCLASSIFIED
PFMEA plays a crucial role in identifying, prioritizing, and addressing potential risks within a process. It helps organizations:
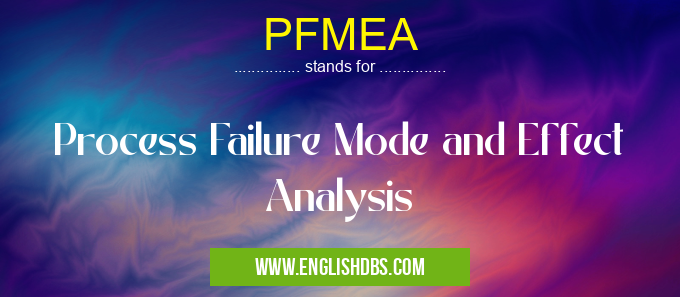
PFMEA meaning in Unclassified in Miscellaneous
PFMEA mostly used in an acronym Unclassified in Category Miscellaneous that means Process Failure Mode and Effect Analysis
Shorthand: PFMEA,
Full Form: Process Failure Mode and Effect Analysis
For more information of "Process Failure Mode and Effect Analysis", see the section below.
Importance of PFMEA
- Enhance product quality and reliability
- Reduce the likelihood of failures and accidents
- Improve process efficiency and safety
- Comply with regulatory requirements
- Identify areas for improvement and optimization
Methodology
PFMEA is conducted in a structured manner, typically following these steps:
- Define the process: Clearly identify the process and its scope to be analyzed.
- Identify failure modes: Brainstorm and document potential ways in which the process could fail.
- Assess failure effects: Determine the consequences of each failure mode, including its impact on customers, products, and the organization.
- Assign severity ratings: Evaluate the potential severity of each failure effect on a scale from 1 (minor) to 10 (catastrophic).
- Identify failure causes: Explore the root causes that could lead to each failure mode.
- Assign occurrence ratings: Estimate the likelihood of each failure cause occurring on a scale from 1 (unlikely) to 10 (frequent).
- Calculate risk priority number (RPN): Multiply the severity, occurrence, and detection ratings for each failure mode to prioritize risks.
- Develop corrective actions: Identify and implement actions to eliminate or mitigate identified risks.
Essential Questions and Answers on Process Failure Mode and Effect Analysis in "MISCELLANEOUS»UNFILED"
What is PFMEA?
PFMEA (Process Failure Mode and Effect Analysis) is a systematic approach to identifying, analyzing, and mitigating potential failures within a manufacturing process. It focuses on preventing failures from occurring rather than detecting them after they happen.
What are the main steps involved in PFMEA?
PFMEA involves several key steps, including defining the process, identifying potential failure modes, evaluating their severity, occurrence, and detection, determining risk priority numbers (RPNs), and implementing corrective actions to mitigate risks.
What is the purpose of PFMEA?
PFMEA aims to improve process reliability, enhance product quality, reduce manufacturing costs, and ensure customer satisfaction by identifying and mitigating potential failures proactively.
Who should participate in a PFMEA team?
A PFMEA team typically includes process engineers, production personnel, quality control specialists, and other relevant stakeholders with knowledge and expertise in the process being analyzed.
What are the benefits of using PFMEA?
PFMEA offers numerous benefits, such as improved process efficiency, reduced downtime, enhanced product reliability, increased customer satisfaction, and compliance with industry standards and regulations.
How can PFMEA be integrated into a quality management system?
PFMEA can be effectively integrated into a quality management system by aligning it with other quality tools and techniques, such as Six Sigma, lean manufacturing, and statistical process control.
What are the limitations of PFMEA?
While PFMEA is a powerful tool, it has certain limitations, including the potential for bias in risk assessment, the assumption of independence between failure modes, and the need for continuous monitoring and updating.
Final Words: PFMEA is a valuable tool for organizations seeking to minimize risks, improve process outcomes, and ensure the safety and quality of their products and services. By proactively identifying and addressing potential failures, PFMEA enables organizations to enhance their operational efficiency, reduce costs, and foster a culture of continuous improvement.