What does SCAR mean in MANAGEMENT
SCAR stands for Supplier Corrective Action Request. It is a formal document issued by a customer to a supplier, requesting corrective action for a nonconforming product or service. The purpose of a SCAR is to identify and address the root cause of the nonconformity and to prevent its recurrence.
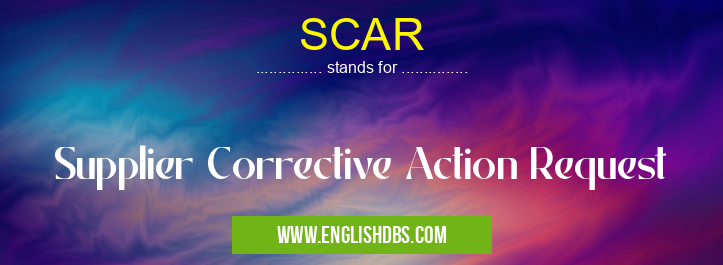
SCAR meaning in Management in Business
SCAR mostly used in an acronym Management in Category Business that means Supplier Corrective Action Request
Shorthand: SCAR,
Full Form: Supplier Corrective Action Request
For more information of "Supplier Corrective Action Request", see the section below.
» Business » Management
Elements of a SCAR
A typical SCAR includes the following elements:
- Identification of the nonconforming product or service: This includes a detailed description of the nonconformity, including the quantity, lot number, and date of receipt.
- Description of the corrective action required: This specifies the actions that the supplier must take to correct the nonconformity. The corrective action should be specific, measurable, achievable, relevant, and time-bound (SMART).
- Timeline for corrective action: This establishes the deadline by which the supplier must complete the corrective action.
- Verification of corrective action: This outlines the steps that the customer will take to verify that the corrective action has been implemented effectively and the nonconformity has been resolved.
Process for Issuing a SCAR
The process for issuing a SCAR typically involves the following steps:
- Identification of the nonconformity: The customer identifies a nonconforming product or service received from the supplier.
- Investigation of the nonconformity: The customer investigates the nonconformity to determine its root cause.
- Issuance of the SCAR: The customer issues a SCAR to the supplier, outlining the nonconformity, the required corrective action, and the timeline for completion.
- Supplier response: The supplier investigates the nonconformity, develops a corrective action plan, and submits it to the customer for approval.
- Implementation of corrective action: The supplier implements the approved corrective action plan.
- Verification of corrective action: The customer verifies that the corrective action has been implemented effectively and the nonconformity has been resolved.
Essential Questions and Answers on Supplier Corrective Action Request in "BUSINESS»MANAGEMENT"
What is a Supplier Corrective Action Request (SCAR)?
A SCAR is a formal request to a supplier to take corrective action to address a nonconformance, defect, or other issue with a product or service. It is typically issued when a supplier's performance fails to meet agreed-upon standards or specifications.
When should a SCAR be issued?
A SCAR should be issued when a supplier's performance does not meet expectations and the issue cannot be resolved through informal communication. This may include situations such as:
- Nonconforming products or services
- Missed delivery deadlines
- Quality defects
- Failure to meet contractual obligations
What should be included in a SCAR?
A SCAR should include the following information:
- A clear description of the nonconformance or issue
- Specific details about the affected products or services
- Evidence or data supporting the issue (e.g., inspection reports, test results)
- The requested corrective actions to be taken by the supplier
- A timeline for corrective action implementation
- The consequences of non-compliance
What is the process for issuing a SCAR?
The process for issuing a SCAR typically involves the following steps:
- Identify the nonconformance or issue
- Gather evidence and documentation
- Draft the SCAR
- Submit the SCAR to the supplier
- Monitor the supplier's corrective action plan
- Follow up to ensure implementation and effectiveness
What are the benefits of using SCARs?
SCARs provide several benefits, including:
- Improved supplier performance by identifying and addressing nonconformances
- Enhanced product or service quality
- Reduced risk of future issues
- Documentation of supplier corrective actions
- A framework for continuous improvement
Final Words: SCARs are essential tools for managing supplier quality and preventing nonconformities from recurring. By clearly identifying nonconformities and requiring corrective action, customers can ensure that their suppliers meet the required quality standards and that their products and services are reliable and safe. SCARs also foster collaboration between customers and suppliers, promoting continuous improvement and strengthening their business relationships.