What does QCP mean in QUALITY ASSURANCE & CONTROL
Quality Control Plan (QCP) is a comprehensive document that outlines the procedures and standards for ensuring the quality of a product or service. It provides a roadmap for achieving and maintaining consistent quality throughout the production or delivery process.
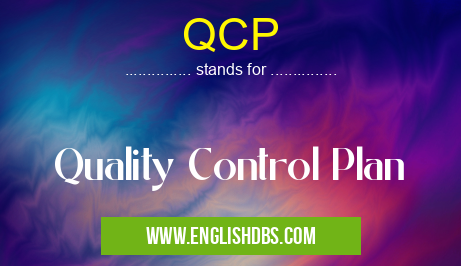
QCP meaning in Quality Assurance & Control in Miscellaneous
QCP mostly used in an acronym Quality Assurance & Control in Category Miscellaneous that means Quality Control Plan
Shorthand: QCP,
Full Form: Quality Control Plan
For more information of "Quality Control Plan", see the section below.
What is a Quality Control Plan (QCP)?
A QCP establishes clear objectives, responsibilities, and methodologies for managing quality. It typically includes:
- Quality Objectives: Specific, measurable, attainable, relevant, and time-bound (SMART) targets for the desired quality of the product or service.
- Inspection and Testing Procedures: Detailed instructions on how to conduct inspections, tests, and measurements to verify compliance with quality standards.
- Acceptance Criteria: Predefined limits or specifications that a product or service must meet to be considered acceptable.
- Corrective and Preventive Actions: Procedures for identifying and addressing quality issues, as well as measures to prevent their recurrence.
- Documentation and Records: Requirements for maintaining records of inspections, tests, and corrective actions to demonstrate compliance and traceability.
Importance and Benefits of QCP
A well-defined QCP is crucial for organizations to:
- Ensure Product/Service Quality: By establishing clear standards and procedures, it helps ensure that products or services meet the desired quality levels.
- Improve Efficiency and Reduce Waste: By preventing defects and identifying potential problems early, it reduces rework, scrap, and other forms of waste.
- Enhance Customer Satisfaction: Consistent quality leads to improved customer satisfaction, loyalty, and repeat business.
- Satisfy Regulatory Requirements: Many industries have regulatory requirements for quality control, and a QCP helps meet these standards.
- Identify Areas for Improvement: By tracking quality data and identifying trends, organizations can pinpoint areas where processes can be improved.
Essential Questions and Answers on Quality Control Plan in "MISCELLANEOUS»QUALITY"
What is a Quality Control Plan (QCP)?
A Quality Control Plan (QCP) is a documented set of instructions that outlines the specific procedures and measures to be taken to ensure the quality of a product or service. It defines the standards, responsibilities, and processes necessary to achieve the desired level of quality.
Why is a QCP important?
A QCP is important because it:
- Ensures that products or services meet customer requirements and expectations.
- Identifies potential quality issues and establishes measures to prevent them.
- Monitors and controls quality throughout the production process.
- Provides documentation of quality control processes for regulatory compliance and traceability.
What are the key elements of a QCP?
The key elements of a QCP typically include:
- Quality standards and objectives
- Inspection and testing procedures
- Measurement and data collection methods
- Responsibilities and authority
- Corrective action procedures
- Documentation and record-keeping requirements.
Who is responsible for developing and implementing a QCP?
The responsibility for developing and implementing a QCP typically lies with the quality management team. However, it requires collaboration and input from various departments, such as production, engineering, and marketing.
How is a QCP reviewed and revised?
A QCP should be regularly reviewed and revised to reflect changes in product specifications, customer requirements, or regulatory standards. The review process typically involves assessing the effectiveness of the plan, identifying areas for improvement, and making necessary updates.
Final Words: Quality Control Plans (QCPs) are essential tools for ensuring the quality of products and services. They provide a systematic approach to managing quality, reducing defects, improving efficiency, and enhancing customer satisfaction. By adhering to QCPs, organizations can establish and maintain consistent quality throughout their operations, leading to greater success and competitiveness in the market.
QCP also stands for: |
|
All stands for QCP |