What does CIM mean in UNCLASSIFIED
CIM stands for Ceramic Injection Moulding. CIM is an advanced manufacturing technique used to produce complex and precise ceramic components. This process involves injecting a ceramic-filled polymer mixture into a mould, where it solidifies and is then heated to remove the binder, leaving behind the final ceramic component.
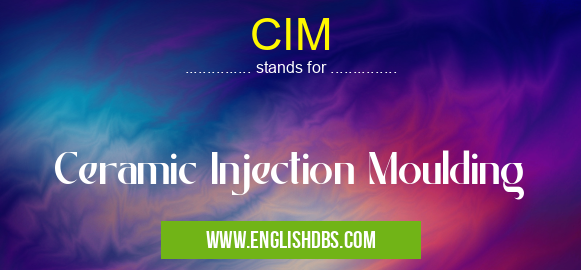
CIM meaning in Unclassified in Miscellaneous
CIM mostly used in an acronym Unclassified in Category Miscellaneous that means Ceramic Injection Moulding
Shorthand: CIM,
Full Form: Ceramic Injection Moulding
For more information of "Ceramic Injection Moulding", see the section below.
Process of CIM
- Feedstock Preparation: A mixture of ceramic powder, binder (typically a thermoplastic polymer), and additives is prepared.
- Injection Moulding: The feedstock is injected into a mould cavity under pressure, forming the desired shape.
- Binder Removal: The binder is removed from the moulded part through a process called debinding, which can involve solvent extraction or thermal decomposition.
- Sintering: The debinded part is heated to high temperatures, typically above 1000°C, to fuse the ceramic particles and create a dense and strong component.
Advantages of CIM
- Complex Geometries: CIM allows for the production of intricate and complex ceramic shapes that are difficult or impossible to achieve with traditional methods.
- Dimensional Accuracy: The injection moulding process ensures high precision and dimensional accuracy in the final components.
- Near-Net-Shape: CIM reduces the need for extensive post-processing, as the parts are formed close to their final shape.
- High Volume Production: CIM enables the mass production of ceramic components with consistent quality and performance.
Applications of CIM
- Aerospace and Defence: High-performance ceramic components for turbine blades, nozzles, and engine parts.
- Automotive: Wear-resistant components, such as brake pads and piston rings.
- Electronics: Substrates, packages, and electronic devices with precise dimensions.
- Medical: Implants, surgical tools, and dental restorations.
Essential Questions and Answers on Ceramic Injection Moulding in "MISCELLANEOUS»UNFILED"
What is Ceramic Injection Moulding (CIM)?
CIM is a manufacturing process that combines injection moulding techniques with ceramic materials. It involves injecting a ceramic-filled feedstock into a mould, where it solidifies and forms the desired shape.
What are the advantages of CIM?
CIM offers several advantages, including:
- High precision and dimensional accuracy
- Complex geometry capabilities
- Near-net-shape manufacturing, reducing machining needs
- Mass production capabilities
What materials are used in CIM?
CIM feedstocks typically consist of a ceramic powder blended with a binder system. Common ceramic materials include alumina, zirconia, and silicon nitride. The binder system holds the powder particles together during injection moulding and is removed during a subsequent debinding and sintering process.
What are the steps involved in CIM?
The CIM process generally includes the following steps:
- Feedstock preparation: Mixing ceramic powder with binder
- Injection moulding: Injecting the feedstock into a mould
- Debinding: Removing the binder through thermal or solvent processes
- Sintering: High-temperature treatment to fuse the ceramic particles and achieve densification
What applications are suitable for CIM?
CIM is widely used in various industries, including:
- Aerospace
- Biomedical
- Electronics
- Automotive
Final Words: CIM is a versatile manufacturing technique that offers significant advantages for the production of complex and precise ceramic components. Its ability to create intricate shapes, achieve high dimensional accuracy, and enable near-net-shape production makes it a valuable tool in various industries.
CIM also stands for: |
|
All stands for CIM |