What does LFL mean in UNCLASSIFIED
LFL involves producing or procuring only the exact quantity of goods needed to fulfill current demand. This is achieved by closely monitoring inventory levels and demand patterns to ensure that production or procurement aligns with actual consumption. By following the LFL principle, businesses can minimize waste, reduce inventory carrying costs, and improve overall supply chain efficiency.
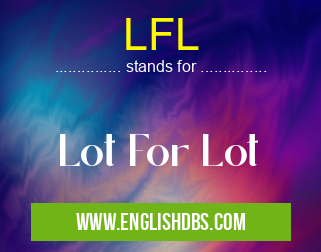
LFL meaning in Unclassified in Miscellaneous
LFL mostly used in an acronym Unclassified in Category Miscellaneous that means Lot For Lot
Shorthand: LFL,
Full Form: Lot For Lot
For more information of "Lot For Lot", see the section below.
How LFL Works
Benefits of LFL
- Reduced Inventory Costs: LFL helps businesses maintain lower inventory levels, reducing the associated costs of storage, handling, and insurance.
- Minimized Waste: By producing or acquiring only what is needed, LFL prevents overproduction and potential waste.
- Improved Cash Flow: Lower inventory levels free up cash that can be used for other business activities.
- Increased Productivity: LFL streamlines production processes by eliminating unnecessary steps and reducing downtime caused by overproduction.
- Improved Customer Service: LFL enables businesses to meet demand more effectively, leading to reduced lead times and improved customer satisfaction.
Essential Questions and Answers on Lot For Lot in "MISCELLANEOUS»UNFILED"
What is Lot For Lot (LFL)?
Lot For Lot (LFL) is an inventory management technique where each individual unit of inventory is tracked and managed separately. Each unit is assigned a unique identifier, such as a serial number or batch number, and its movement through the supply chain is recorded.
What are the benefits of using LFL?
LFL provides several benefits, including:
- Improved inventory accuracy
- Reduced inventory shrinkage
- Enhanced product traceability
- Increased efficiency in warehouse operations
- Improved control over inventory costs
How is LFL implemented?
Implementing LFL typically involves the following steps:
- Assigning unique identifiers to each unit of inventory
- Establishing a system for tracking the movement of each unit
- Integrating LFL with other inventory management systems
- Training staff on LFL procedures
What industries use LFL?
LFL is commonly used in industries where inventory management is critical, such as:
- Pharmaceuticals
- Electronics
- Aerospace
- Automotive
- Food and beverage
What are the challenges of implementing LFL?
Implementing LFL can present some challenges, including:
- High implementation costs
- Complex integration with existing systems
- Potential for increased labor costs
- Need for rigorous data management
Final Words: LFL is a valuable technique for businesses seeking to optimize their supply chains and improve overall efficiency. By aligning production or acquisition with actual demand, LFL helps minimize waste, reduce inventory costs, and enhance customer service. Implementing LFL requires careful planning and coordination, but the benefits it brings can significantly contribute to a business's bottom line and competitive advantage.
LFL also stands for: |
|
All stands for LFL |