What does DOPP mean in PREVENTION
Dropped Object Prevention Program (DOPP) is a company program that strives to prevent the accidental dropping of objects in the workplace, with the goal of reducing risk and ensuring safety for all employees and customers. By following best practices and implementing measures such as inspections, storage, and tool management protocols, DOPP can minimize the risks associated with dropped objects.
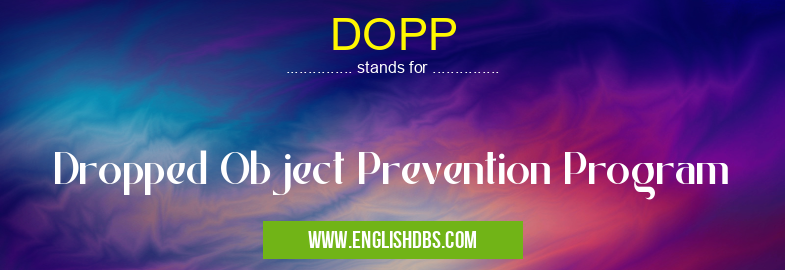
DOPP meaning in Prevention in Medical
DOPP mostly used in an acronym Prevention in Category Medical that means Dropped Object Prevention Program
Shorthand: DOPP,
Full Form: Dropped Object Prevention Program
For more information of "Dropped Object Prevention Program", see the section below.
» Medical » Prevention
What is DOPP?
DOPP is a systematic approach to avoiding dropped object incidents at worksites. It involves identifying potential hazards that could lead to a dropped object incident, implementing preventive measures to reduce or eliminate those hazards and conducting regular inspections on equipment and personnel to ensure that these preventive measures are meeting their intended purpose. Additionally, DOPP includes educating personnel on safe work practices around dropped objects so that any occurrence can be quickly and safely handled in order to minimize the risk of injury or harm.
Preventive Measures
DOPP utilizes various mechanisms designed to help recognize and avoid potential dropped objects situations. These may include visual management tools such as signposting areas that are prone to more frequent droppings; use of mechanical engineering controls such as designed barriers in high-risk areas; use of ergonomic aids such as reach aids or extended handles; providing appropriate personal protective equipment (PPE) for personnel; storage protocols specifically designed with consideration of location and size of item being stored; and implementation of proactive inspection programs across all worksites. All these measures are aimed at preventing or minimizing the number of accidents caused by dropped objects.
Concluding Thoughts
The Dropped Object Prevention Program promises improved safety in workplaces by implementing preventive measures that minimize potential danger from dropped items such as pipes, tools, riggers etc., thus preventing losses related to downtime due to injury or worse. Adequate implementation of DOPP standards will further ensure compliance with relevant safety regulations which enhances safety for personnel handling operations within industrial environments.
Essential Questions and Answers on Dropped Object Prevention Program in "MEDICAL»PREVENTION"
What is DOPP?
DOPP stands for "Dropped Object Prevention Program," a program designed to reduce the risk of dropped objects in the workplace. It works by identifying at-risk areas and implementing preventative measures, such as improved storage, regular inspections of equipment, and safety training.
Who is responsible for implementing the DOPP?
The implementation and maintenance of the DOPP is typically the responsibility of an appointed Safety Officer or team within an organization. This person or team will create a plan to ensure that all risks are identified and remedied in a timely fashion.
In what types of workplaces does DOPP apply?
The DOPP applies to any workplace where dropped objects may pose a hazard - this includes factories, warehouses, construction sites, oil rigs, and other industries with elevated work or heavy machinery.
How can I identify areas where dropped objects are a risk?
To identify areas where dropped objects may be a risk, you should consider the potential height of an object drop, the type of material being dropped (sharp edges vs. blunt force), any existing housekeeping hazards in the area that could further increase potential danger if struck by a falling object, and any known incidents of people dropping tools/objects in the past.
What safety measures should be taken when working with elevated tools/equipment?
When working with elevated tools/equipment it's important to take certain precautions - this includes wearing personal protective equipment (PPE) such as safety goggles and gloves; regularly inspecting tools for damage; using handrails when necessary; properly securing ladders; using proper lifting techniques; always following manufacturer's instructions; and ensuring that all staff receive relevant training on how to safely use tooling & equipment.
What can employers do reduce the risk of dropped objects?
Employers can reduce the risk of dropped objects by creating clear policies for working at height; conducting regular risk assessments and inspections; providing adequate PPE for staff; installing barriers around equipment & machinery where necessary; consolidating tools into toolboxes whenever possible; coding & labeling items so they can easily be identified; providing proper storage spaces for items not in use; doing frequent maintenance on tools & equipment to ensure they are functioning properly; and ensuring all staff receive appropriate training on safe working practices.
Are there any regulations that need to be followed regarding prevention of dropped objects?
Different countries have different regulations regarding prevention of dropped objects - however most countries have laws in place requiring employers to provide reasonable protection against injuries caused by hazardous conditions or activities onsite, including those related to droppable objects. Check your local laws for specific requirements relevant to your operations.
Are there any repercussions if employers fail to comply with DOPP regulations?
In most cases non-compliance with DOPP regulations can result in serious repercussions from government authorities - including fines, suspensions or even closures depending on the severity of non-compliance issues observed by inspectors.
Is there any additional guidance available related to Dropped Object Prevention programs?
Yes, many organizations offer additional guidance documents related specifically to Dropped Object Prevention Programs - these typically include best practices developed through decades of research into what works best when it comes preventative measures against drops occurring within workplaces. Such documents are available from various industry associations or online sources.
How often should I audit my DOPP program?
It's recommended that workplaces audit their DOPP plan regularly — at least once per month depending on how rigorous their other safety protocols & procedures are — as well as after major changes occur within the workplace (e.g., new staff members joining). This helps ensure that all safety protocols remain up-to-date & effective wherever possible.
Can I get help setting up my own Dropped Object Prevention Program?
Yes! Many companies offer consulting services related specifically towards developing comprehensive Dropped Object Prevention Programs tailored precisely towards each organization's unique needs & objectives - contact them directly either through their website or via email/phone inquiries for more information about how they could help you set up your own program.