What does LMOS mean in BUSINESS
Lean Management Operation System (LMOS) is a comprehensive approach to optimizing business operations and improving efficiency. By focusing on value-added activities, LMOS eliminates waste and streamlines processes to enhance productivity and customer satisfaction.
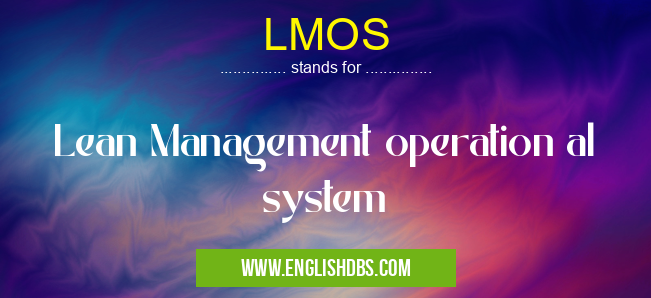
LMOS meaning in Business in Business
LMOS mostly used in an acronym Business in Category Business that means Lean Management operation al system
Shorthand: LMOS,
Full Form: Lean Management operation al system
For more information of "Lean Management operation al system", see the section below.
LMOS Meaning in BUSINESS
LMOS is a systematic framework that encompasses various elements of lean management, such as:
- Value Stream Mapping: Identifying and analyzing the flow of activities to eliminate bottlenecks and non-value-added steps.
- Continuous Improvement (Kaizen): Iteratively identifying and addressing areas for improvement, fostering a culture of ongoing optimization.
- Standard Operating Procedures (SOPs): Establishing clear and consistent work instructions to reduce variability and improve quality.
- Visual Management: Utilizing visual aids such as charts, boards, and dashboards to track progress and identify potential issues.
- Employee Engagement: Empowering employees to contribute to improvement efforts and fostering a sense of ownership.
Benefits of LMOS
By implementing LMOS, businesses can reap numerous benefits, including:
- Reduced waste and improved resource utilization
- Increased efficiency and productivity
- Enhanced customer satisfaction
- Improved quality and reduced defects
- Increased flexibility and adaptability
- Improved communication and collaboration
Essential Questions and Answers on Lean Management operation al system in "BUSINESS»BUSINESS"
What is LMOS?
LMOS stands for Lean Management Operating System, a comprehensive framework that incorporates lean principles and tools to improve operational efficiency and performance.
What are the key components of LMOS?
LMOS consists of five core elements: Visual Management, Daily Management, Standard Work, Kaizen, and Hoshin Kanri. Each component plays a specific role in identifying and eliminating waste, improving processes, and empowering employees.
How does LMOS benefit organizations?
By implementing LMOS, organizations can experience numerous benefits, including:
- Increased productivity and efficiency
- Reduced waste and costs
- Improved quality and customer satisfaction
- Enhanced employee engagement and morale
- Greater adaptability to changing market demands
How can organizations implement LMOS?
Implementing LMOS requires a structured approach and commitment from leadership. Organizations typically follow these steps:
- Establish a clear vision and goals
- Train employees on lean principles and tools
- Implement core LMOS elements
- Monitor progress and make adjustments as needed
What are some examples of LMOS in practice? A: Organizations that have successfully implemented LMOS include: - Toyot
Organizations that have successfully implemented LMOS include:
- Toyota: Uses LMOS to drive operational efficiency in its manufacturing plants
- Amazon: Leverages LMOS to improve inventory management and fulfillment processes
- Google: Implements LMOS to enhance collaboration and productivity in its software development teams
Final Words: LMOS is a powerful tool that empowers businesses to achieve operational excellence. By eliminating waste, streamlining processes, and fostering continuous improvement, LMOS helps organizations enhance their competitiveness, increase profitability, and deliver exceptional customer experiences. Embracing the principles of LMOS can transform business operations and drive sustained success.