What does IBRE mean in UNCLASSIFIED
IBRE stands for Ion Bombardment Retarded Etching. It is a technique used in semiconductor fabrication to etch (remove) material from a substrate surface precisely. This process involves bombarding the substrate with ions, typically argon or xenon, to remove atoms or molecules from the surface.
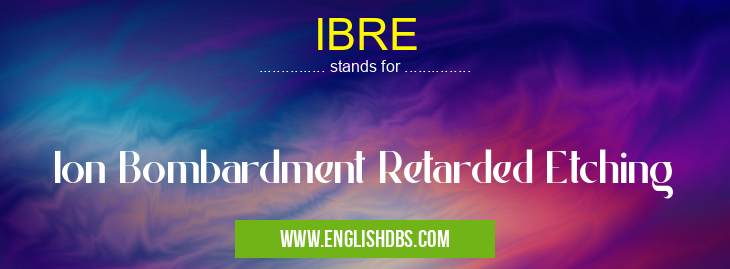
IBRE meaning in Unclassified in Miscellaneous
IBRE mostly used in an acronym Unclassified in Category Miscellaneous that means Ion Bombardment Retarded Etching
Shorthand: IBRE,
Full Form: Ion Bombardment Retarded Etching
For more information of "Ion Bombardment Retarded Etching", see the section below.
Process
IBRE utilizes a highly energetic ion beam directed at the substrate surface. The ions impact the surface, transferring energy and momentum to the atoms or molecules on the surface. This energy transfer causes the atoms or molecules to be ejected from the surface, resulting in etching.
Advantages
- High Precision: IBRE offers precise control over the etching process, allowing for precise patterning and feature definition.
- Anisotropic Etching: The ions in IBRE can be directed perpendicular to the substrate surface, resulting in anisotropic etching, where the material is removed vertically rather than laterally.
- Low Damage: IBRE uses low-energy ions, minimizing damage to the substrate material.
- Scalability: IBRE is scalable to large-area processing, making it suitable for industrial applications.
Applications
IBRE is widely used in semiconductor fabrication for:
- Etching of silicon, silicon nitride, and metal films.
- Patterning of resist materials.
- Removal of unwanted material during device processing.
Essential Questions and Answers on Ion Bombardment Retarded Etching in "MISCELLANEOUS»UNFILED"
What is Ion Bombardment Retarded Etching (IBRE)?
Ion Bombardment Retarded Etching (IBRE) is a technique used in the semiconductor industry to create precise patterns and structures in thin films. It involves bombarding a target surface with ions while simultaneously etching the surface with a reactive gas. This process combines physical sputtering and chemical etching to achieve high-resolution patterns.
How does IBRE work?
In IBRE, a beam of ions is directed at the target surface. These ions collide with the surface atoms, transferring their energy and causing the atoms to be ejected (sputtered). Simultaneously, a reactive gas is introduced into the chamber, which reacts with the sputtered atoms and etches the surface. The etching rate is controlled by the energy of the ions and the type of reactive gas used.
What are the advantages of IBRE?
IBRE offers several advantages compared to conventional etching techniques:
- High precision: IBRE allows for the creation of highly precise patterns and structures with submicron resolution.
- Anisotropic etching: The process produces vertical sidewalls and minimal undercutting, resulting in high-quality etched features.
- Controllable etch depth: The etch depth can be precisely controlled by varying the ion energy and exposure time.
- Damage reduction: IBRE minimizes surface damage compared to other etching methods, preserving the integrity of the underlying material.
What types of materials can be etched using IBRE?
IBRE can be used to etch a wide range of materials, including metals, semiconductors, ceramics, and polymers. It is commonly used in the fabrication of microelectronics, photonics, and MEMS devices.
What are the limitations of IBRE?
IBRE has some limitations, such as:
- High cost: The equipment and materials required for IBRE can be expensive.
- Slow etching rate: The process can be relatively slow compared to other etching techniques.
- Low etch selectivity: IBRE may not be selective for certain materials, requiring additional processing steps to achieve the desired results.
Final Words: IBRE is a highly precise and versatile etching technique used in semiconductor fabrication. Its advantages include high precision, anisotropic etching, low damage, and scalability, making it a valuable tool for advanced device manufacturing.