What does FPOC mean in CONTACT
FPOC stands for Factory Point of Contact. It is a term used in the manufacturing industry to refer to the primary contact person at a factory who is responsible for communication and coordination with external parties, such as suppliers, customers, and logistics providers.
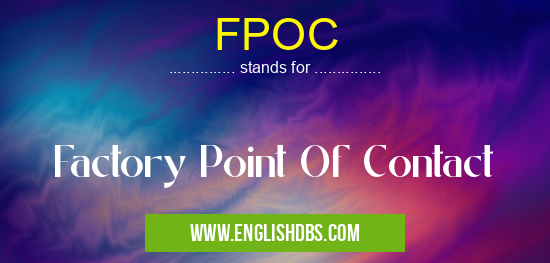
FPOC meaning in Contact in Contact
FPOC mostly used in an acronym Contact in Category Contact that means Factory Point Of Contact
Shorthand: FPOC,
Full Form: Factory Point Of Contact
For more information of "Factory Point Of Contact", see the section below.
Responsibilities of an FPOC
The FPOC typically handles a wide range of tasks, including:
- Communicating with suppliers and customers to coordinate orders, track shipments, and resolve any issues
- Providing updates on production status and lead times
- Managing logistics, including scheduling deliveries and coordinating with carriers
- Answering inquiries and providing customer support
- Maintaining relationships with key stakeholders
Benefits of Having an FPOC
Establishing a designated FPOC offers several benefits:
- Improved Communication: A centralized point of contact ensures smooth and efficient communication between all relevant parties.
- Efficient Coordination: The FPOC can coordinate activities between departments within the factory and external entities, streamlining processes.
- Reduced Errors: By having a single point of contact, confusion and errors are minimized.
- Enhanced Customer Service: A dedicated FPOC can provide prompt and responsive support to customers, fostering positive relationships.
Essential Questions and Answers on Factory Point Of Contact in "CONTACT»CONTACT"
What is the role of a Factory Point of Contact (FPOC)?
An FPOC is the primary contact person for a manufacturer or supplier. They assist buyers with inquiries, order processing, and other factory-related matters.
How can I contact the FPOC for a specific factory?
FPOC contact information can typically be found on the factory's website, purchase orders, or through the purchasing department of the buyer's company.
What are the responsibilities of an FPOC?
FPOCs are responsible for:
- Answering queries and providing information
- Processing orders and ensuring timely delivery
- Monitoring production and quality
- Coordinating with buyers and other internal departments
- Resolving any issues or concerns
How can buyers benefit from working with an FPOC?
Engaging with an FPOC offers buyers:
- Direct access to factory representatives
- Quick response to inquiries and order-related matters
- Improved communication and transparency
- Timely updates on production status and delivery timelines
- Assistance with resolving any factory-related issues
What qualities should buyers look for in an FPOC?
Buyers should seek FPOCs who are:
- Knowledgeable about the factory's capabilities and products
- Responsive and proactive in communication
- Efficient and organized in order processing
- Able to resolve issues effectively
Is it always necessary to communicate directly with the FPOC?
While it is generally recommended to communicate directly with the FPOC, buyers may also work with other factory personnel depending on the specific task or situation.
Final Words: The FPOC plays a crucial role in the manufacturing supply chain by facilitating communication, coordinating activities, and providing support. By establishing a clear and reliable FPOC, manufacturers can improve their operations, enhance customer satisfaction, and drive efficiency throughout their processes.
FPOC also stands for: |
|
All stands for FPOC |