What does WDFR mean in MILITARY
WDFR stands for Worst Damage First Repair. It is a policy and procedure implemented by various governments around the world to prioritize public infrastructure repairs and maintenance. This policy ensures that the most serious, large scale, and complex areas of damage are repaired before any lesser damages. By doing this, it helps avoid further deteriorating of infrastructure and ensures safety of citizens in affected areas. In other words, WDFR is a strategy used to minimize the repairs required for a particular infrastructure after an event such as natural disaster
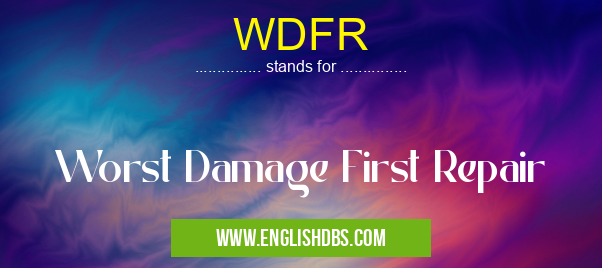
WDFR meaning in Military in Governmental
WDFR mostly used in an acronym Military in Category Governmental that means Worst Damage First Repair
Shorthand: WDFR,
Full Form: Worst Damage First Repair
For more information of "Worst Damage First Repair", see the section below.
» Governmental » Military
Essential Questions and Answers on Worst Damage First Repair in "GOVERNMENTAL»MILITARY"
What is WDFR?
WDFR stands for Worst Damage First Repair. It's a system used to prioritize repair and maintenance tasks in order to maximize efficiency and minimize downtime. The idea behind it is that the most severely damaged components should be fixed first, while relatively minor issues can wait until later. This ensures that efficiency is at its highest and downtime is kept to a minimum.
How does WDFR work?
The WDFR system works by assessing the severity of damages and prioritizing repairs from most severe to least severe. This allows technicians to efficiently tend to the most important jobs first, leaving less essential ones for later when there’s more time available.
Who uses WDFR?
WDFR is utilized by professionals in various industries including automotive repair, medical equipment maintenance, HVAC maintenance, aircraft service, electronics repair, and more. Any situation where timely repairs can reduce downtime or prevent major failure can benefit from using the WDFR system.
What are the benefits of using WDFR?
By leveraging this system, technicians can identify areas needing urgent attention quickly so they can swiftly address them prior to any further damage occurring. Additionally, it helps optimize workflow since technicians are able to focus on highly important tasks first before tackling minor issues later on. In the end, this not only saves time but also ensures that repairs are done right the first time around.
What types of damages should be considered when using WDFR?
When utilizing this technique, damages like faulty parts or components with signs of corrosion should be addressed as soon as possible due to their ability to cause productive loss or permanently disable machinery if left unchecked for too long. Minor problems such as small chips or scratches may be better handled after more serious damages have been addressed first.
How much lead time is needed for an effective implementation of WDFR?
It depends largely on the complexity of a particular job or situation but usually comprehensive assessment and proactive planning should be conducted well in advance in order for an effective implementation of this strategy. For example simple and straightforward operations may require less lead time than complex multi-component troubleshooting projects which would need longer lead time in order assess all potential risks appropriately.
What type of data must I gather before implementing WDFR?
Before utilizing this method you will need to gather relevant data related your operation such as detailed information about components used on site, available spare parts inventory list (if any), past troubleshooting reports (if any) and other relevant technical documents associated with malfunctioning parts as required.
Can WFDR help enhance customer experience?
Absolutely! By minimizing costly delays due to inefficient repairs caused by heavy workloads resulting from improper repair scheduling; customers will receive much smoother service experiences which can go along way towards creating a favorable impression regarding overall quality and reliability.
: Is there any training requirement in order implement WFDR effectively?
: Yes! Proper training is imperative since proper utilization demands specialist knowledge on various topics such as lamination techniques , soldering skills emergency response procedures etc . Before attempting complex tasks one has to make sure that they are well equipped with all necessary tools AND have adequate training for successful implementation of this strategy.