What does IQMP mean in FDA
Integrated Quality Management Plans (IQMPs) are comprehensive and detailed plans used by businesses or organizations in the Government sector to facilitate and maintain quality assurance in their operations. IQMPs work as a road map for any organization that outlines the strategies, protocols, and management procedures essential for successful quality assurance. The primary objective of an IQMP is to improve the overall efficiency of an organization through a thorough evaluation of its objectives, resources, standards, risks and processes. This article will explain what an IQMP is, its meaning in the Government sector, and what it stands for.
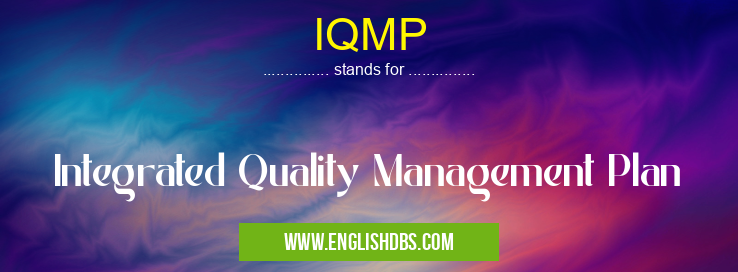
IQMP meaning in FDA in Governmental
IQMP mostly used in an acronym FDA in Category Governmental that means Integrated Quality Management Plan
Shorthand: IQMP,
Full Form: Integrated Quality Management Plan
For more information of "Integrated Quality Management Plan", see the section below.
» Governmental » FDA
Meaning In Governmental
In Governmental sectors such as public administrations or governmental agencies there is often a need to ensure high-quality services or products remain consistent over time. This is why Integrated Quality Management Plans are often used in this context since they provide important information about how best to manage organizational resources, set achievable goals and effectively communicate with stakeholders involved in the process such as customers or suppliers. An IQMP typically contains specific details about core elements such as quality objectives, risk mitigation strategies, performance metrics and customer service standards. On top of that, it can include additional requirements depending on the nature or scope of work conducted by a particular agency or organization which further aids with establishing effective control over organizational procedures.
IQMP Full Form
The full form for Integrated Quality Management Plan is “IQMP”; this acronym gives succinctly summarizes its purpose -integrating quality management into all aspects related to an organization’s functioning including resource allocation & utilization, decision making, product & service design, process performance monitoring & evaluation, customer satisfaction benchmarks etc. It ensures that all departments adhere to pre-defined protocols & processes while aligning them with administrative & legal requirements. As a result, it helps organizations develop effective communication strategies & prevent costly errors resulting from lack thereof.
Essential Questions and Answers on Integrated Quality Management Plan in "GOVERNMENTAL»FDA"
What is an Integrated Quality Management Plan (IQMP)?
An Integrated Quality Management Plan (IQMP) is a comprehensive system designed to coordinate, organize, measure and improve quality processes throughout a business. It includes specific plans and activities aimed at ensuring that products meet customer requirements as efficiently and cost effectively as possible. The IQMP draws upon the principles of Total Quality Management (TQM) and applies them to all aspects of the business from customer service to product design.
Why is an IQMP important?
An IQMP is important because it allows businesses to identify potential quality problems before they result in costly losses. By proactively addressing quality issues before they become bigger issues, businesses can save money on repairs, re-work and dissatisfied customers. In addition, it helps ensure regulatory compliance and enables businesses to be competitive in the marketplace by delivering consistent high-quality products.
What elements does an IQMP include?
An IQMP typically includes operations processes such as design, production, engineering, inspection and quality assurance; elements like policies, objectives and standards; activities related to scheduling and resource management; reporting structures; and continuous improvement approaches such as Lean Six Sigma or Kaizen.
How can you benefit from implementing an IQMP?
Companies can benefit from implementing an IQPM in several ways including improving their customer satisfaction levels by ensuring that products meet their requirements; reducing costs associated with waste, re-work or unplanned downtime; becoming more efficient through improved process systems; increasing profits due to higher quality products; faster cycle times for product delivery; better employee morale through recognition for improved performance.
How do you develop an effective integrated quality management plan (IQMP)?
Developing a successful IQMP requires setting clear objectives that are aligned with the company’s mission statement. It should also include understanding customer needs & expectations and determining which processes need to be improved & monitored. Other steps in developing a successful plan may include mapping current processes & flowcharts; establishing measurable goals & KPIs & involving top management through feedback loops & executive reviews.
What factors should be taken into consideration when creating an effective IQPM?
When creating an effective IQPM there are several key factors that should be taken into account such as understanding customer needs & expectations; aligning the plan with overall organizational goals & values; setting measurable goals & KPIs; identifying areas for improvement within existing processes & designing corrective actions if necessary; creating feedback loops between top management and staff members involved in achieving results; fostering a culture of continuous learning through training initiatives.
What roles do different departments play in the development of an effective IQPM?
Different departments have different roles when it comes to developing an effective integrated quality management plan (IQPM). The Human Resources department is responsible for training employees on how to properly use the system while Operations handles logistics related tasks such as equipment inspection & maintenance schedules. The Quality Assurance department ensures that processes are adhering to established standards while Production is responsible for oversight of process improvements/initiatives suggested by staff members throughout the organization. Lastly, Finance is responsible for ensuring costs remain within budgeted limits throughout implementation of any changes within the system.
What metrics should be included when measuring success of an Integrated Quality Management System?
Metrics used when measuring success of an Integrated Quality Management System should include indicators such as reduction in scrap/reject rates or amount of rework required during production cycles along with increased throughput times or cost savings related to reducing unnecessary steps during production cycles. Employee satisfaction scores should also be considered alongside customer satisfaction ratings during measurements since these are direct indicators of how well your organization is doing at meeting your customers' needs.
How often should assessment take place while using a integrated quality management system?
Assessment should take place regularly while using a integrated quality management system in order to ensure progress towards organizational objectives remains on track consistently over time rather than merely being one-time events whenever major changes occur within your operational framework or environment.
How can companies use data collected under an Integrated Quality Management System?
Companies can use data collected under an Integrated Quality Management System for many purposes including gaining insights about how well their operations are performing against set targets/goals across various dimensions such as employee performance or cost savings achieved compared with previous periods or benchmarks set elsewhere within their industries/markets.
Final Words:
Integrated Quality Management Plans provide businesses and other governmental entities with the means to ensure highest levels of quality across all operations being undertaken while meeting collective objectives efficiently and cost-effectively. The value an IQPM brings lies not only in its ability to help streamline processes but also maintain customer satisfaction at all times - ultimately aiding both employees & customers alike while yielding optimal results for any given business environment.